Lenticular module filter
The lenticular module filter uses 'lenses' superimposed around a central tube, each lens containing a filter medium similar to filter plates, thus optimising filtration space. These modules are classified into three categories: degreasing, clarifying and sterilising, each adapted to different stages of filtration. The filtration process includes module installation, rinsing, differential pressure monitoring, regeneration, sterilisation and disinfection. For conservation, the modules must be stored in a sterilised environment and rinsed before re-use.
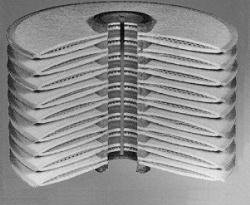
Lenticular module filter
A lenticular module is made up of "lenses" superimposed on the central tube and assembled in such a way as to ensure that the module is watertight. Each lens consists of a filter medium and a drainage system. The filter media is of the same type as the filter plates. The modules are stacked one on top of the other to accommodate the maximum filtering surface in the minimum volume occupied.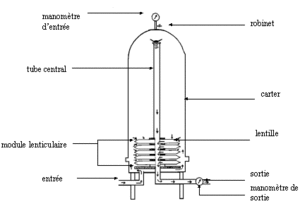
Technical presentation of a lenticular module filter

Cross-section of a lenticular module
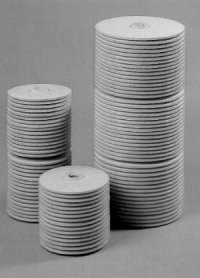
Modules
Main components
The dimensions of the housing depend on the diameter of the modules and the maximum number of modules required. The casing is enclosed, which means that work can be carried out under good hygiene conditions, without aeration or wine leaks.The retention sill
As with filter plates, lenticular modules are classified into 3 categories:- roughing modules
These are designed for pre-filtering new wines to eliminate some of the cloudiness. The filtrate is often not immediately ready for consumption.
These modules have a high filtration rate and are highly efficient. - clarifying modules
These are only used on wines that have been properly stripped, with little cloudiness (only a few NTU or tens of NTU). Used correctly, they significantly reduce the micro-organism population. - sterilising modules
They filter out germs by retaining micro-organisms, yeasts and bacteria. Logically, these modules should be installed before the bottling machine.
Flow rate
This is expressed in hL / h / m².Filter surface per module
This is expressed in m² / module.Choice of number of modules
The number of modules to be installed in the filter depends on the constant flow rate of the filler.Example :
Consider a filter to be installed for a bottling machine working at a rate of 1000 bottles/hour.
The output of the filler is 1000 x 0.75 /100 = 7.5 hL/h.
The minimum surface area of the module to be installed is 7.5 (hL/h) / Flow area (hL/h/m²) = S(m²).
The number of modules is therefore S / Filter area per module.
Filtration pipework
- Installation of the modules.
- Rinsing with water (preferably pre-filtered).
- Filtration: monitor the differential pressure on the pressure gauge. Do not exceed the maximum pressure recommended by the lenticular module manufacturer (generally 1.5 to 2.5 bars).
- Regenerate the filter media using hot water, in the direction of filtration, when the maximum pressure is exceeded and/or at the end of the day.
- Sterilisation with hot water or steam, in the direction of filtration, twice a week.
- Chemical disinfection with sulphuric acid (0.2%) and paracetic acid (0.2%).