Crossflow filter
Tangential filters are mainly used to prepare wines before packaging, offering an alternative to pasteurisation by guaranteeing quality and reducing waste. This process involves the parallel circulation of liquid through a porous membrane, thereby limiting clogging. Different operating configurations (batch, fed batch, in-line) enable the flow and concentration of the filtered wine to be managed efficiently. Membranes can be organic or stainless steel, adapted to different types of wine and impurities. Cross-flow filtration ensures effective clarification and microbiological stabilisation of wines.
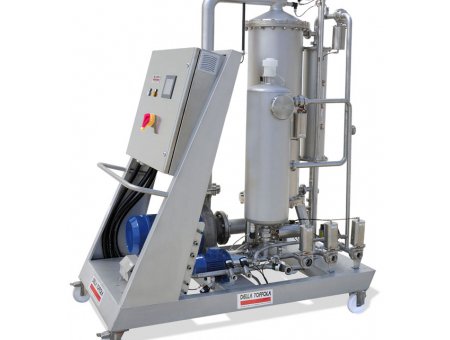
Crossflow filter
Tangential filters are mainly used in the preparation of wines for bottling. Compared with alluvial filtration, tangential microfiltration simplifies the treatment chain, guaranteeing quality while limiting waste production. It is also used for early filtration of wines and as a microbiological stabilisation process, offering an alternative to flash pasteurisation . New configurations allow clarification of products 'laden' with suspended particles, such as musts, lees and tank bottoms.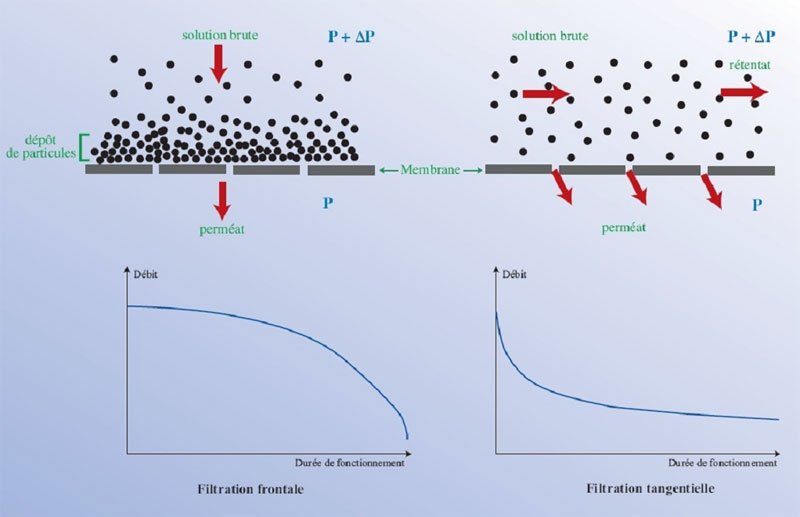
Comparative principles of frontal filtration and cross-flow filtration
The principle involves circulating the liquid to be filtered parallel to a porous membrane. Under the action of pressure, the liquid passes through the membrane and is clarified. The tangential flow creates turbulence that limits the accumulation of particles on the surface of the membrane, thereby delaying clogging.
Main elements
Filter elements
These are membranes integrated into modules. The surface area of each module and the number of modules determine the filtering surface area of the filter.Organic or mineral membranes are used .
Feed pump
Centrifugal or positive displacement with variable flow rate, it supplies and pressurises the fluid.Circulation pump
This creates the flow at the surface of the membrane. Part of the retentate is returned to the feed tank. A valve can be used to regulate the trans-membrane pressure.Feed tank
This may or may not be integrated into the filtration unit.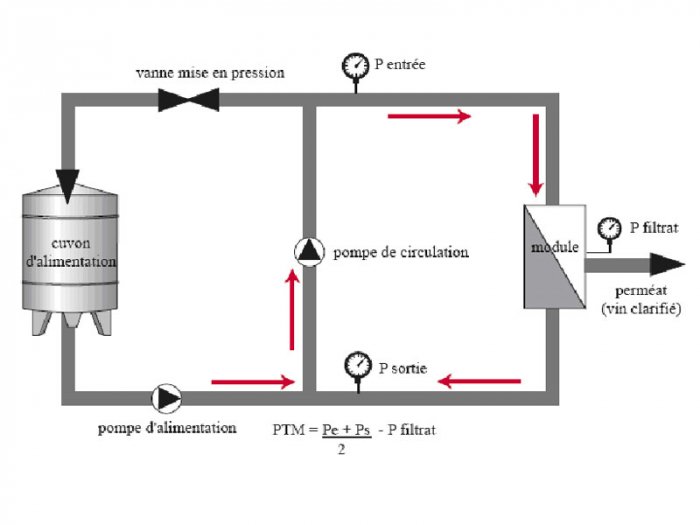
Technical description of the crossflow filter
Loop and pipes
Stainless steel piping, with valves and control and regulation instruments (pressure, flow, temperature, turbidity sensors, etc.).Cleaning device
With the exception of spiral-wound modules, installations are generally equipped with a system for cleaning the membrane during filtration, the most common being periodic reversal of flow, also known as retro-filtration, back-washing or back-wash. Different configurations are available (pneumatic systems, hydraulic systems, backwashing by the filtrate pump).Crossflow filter operation
Different configurations are available. These differences are essentially linked to concentration rate management, automation requirements and installation flow rates.Batch operation
In this configuration, the simplest and least expensive, the retentate is recycled into the feed tank.
This system allows filtration at a low concentration rate (FCV) over the majority of the cycle, to limit membrane clogging.
This system allows filtration at a low concentration rate (FCV) over the majority of the cycle, to limit membrane clogging.
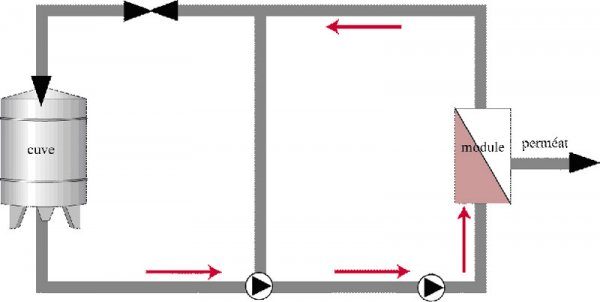
Batch operation
Fed batch operation
The retentate is recycled in a tank integrated into the filtration unit. In this configuration, the FCV increases more quickly than previously, but makes it possible to automate the entire operation.
Depending on the system, the retentate can be concentrated during filtration or only at the end of filtration.
Depending on the system, the retentate can be concentrated during filtration or only at the end of filtration.
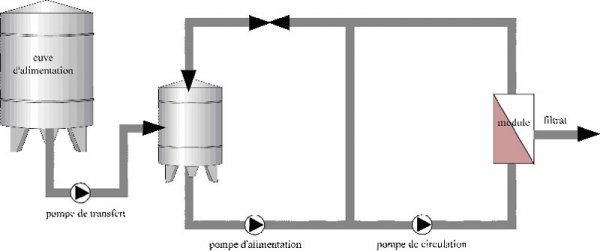
Fed batch operation
In-line operation
A fraction of the retentate is extracted continuously, allowing filtration at low concentration levels.
The retentate is filtered at the end of the filtration cycle (single-stage system) or by a second filter (two-stage system).
The retentate is filtered at the end of the filtration cycle (single-stage system) or by a second filter (two-stage system).
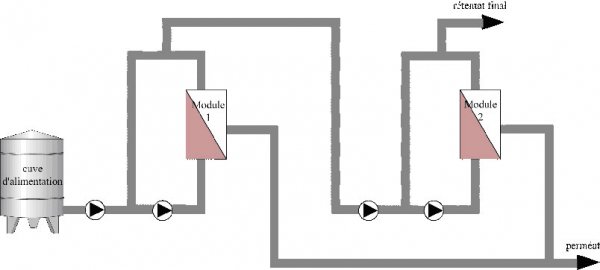
Two-stage system - In-line operation
Special configurations
Tangential Integrated System" process
With this process, each housing containing a module is equipped with its own circulation pump. There is therefore no external circulation loop.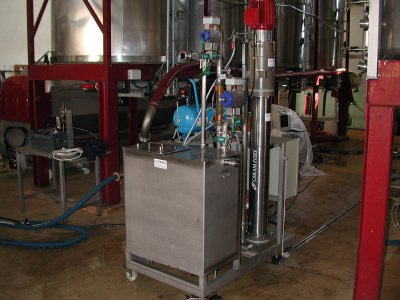
TIS system - Siva Tami
Ceramic single-stage filter

Ceramic single-stage filter - Della Toffola
Organic membranes for clarifying sludge
The filter is equipped with hollow fibre membranes. The special feature is a capillary diameter of 3 mm instead of 1.5 mm. The filter is also equipped with internal scrapers (upper tubing), which keep the liquid flowing smoothly. Upstream, a rotating drum pre-filter removes the largest impurities.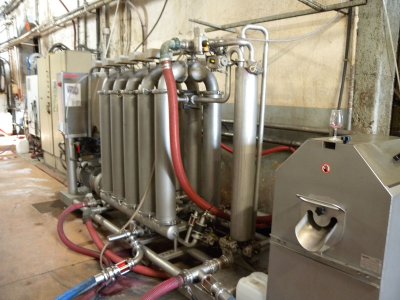
Sludge mode filter - Bucher Vaslin
Organic membranes for lees clarification
The filter is fitted with polyvinylidene fluoride membranes, with large internal diameter hollow fibres.Stainless steel membranes for lees clarification
The filter is fitted with large-diameter tubular membranes, consisting of a sintered stainless steel support and a layer of titanium oxide.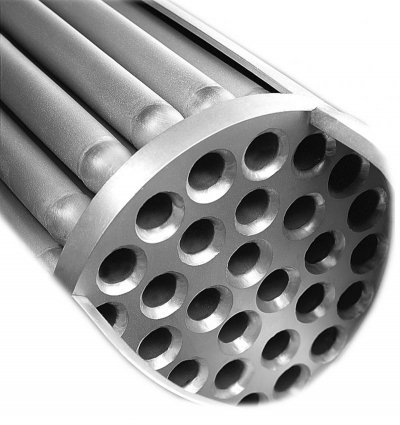
Stainless steel support membrane for lees filtration - Bucher Vaslin
Filter with rotating discs and ceramic membranes
This highly original filter is made up of ceramic disc membranes. The rotation of the discs creates turbulence, limiting membrane clogging.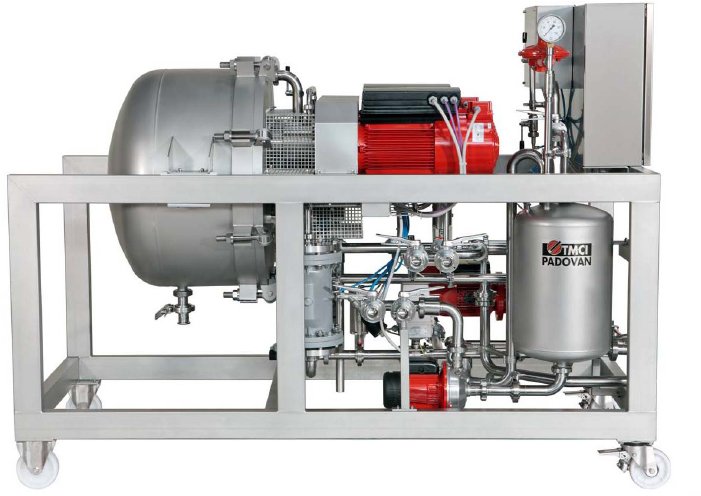
Rotary disc filter - Liatech Padovan
Crossflow filtration
The conditions under which filtration is carried out have a major impact on clogging and therefore on filter performance , both quantitatively (productivity) and qualitatively (colloid and macromolecule retention). Filter operation is generally managedautomatically.Transmembrane pressure
Transmembrane pressure must be kept low, particularly when filtration starts. Increasing the pressure too quickly will lead to rapid, deep-seated membrane clogging.The recommended transmembrane pressures, which vary depending on the design, are generally close to 1 bar (0.5 to 1.5 bar) and it is advisable not to exceed 2 bar at the end of filtration.
Concentration ratio or volume concentration factor (VCF)
In crossflow microfiltration, the higher the dry extract concentration of the product, the lower the flow rate.Temperature of the products to be filtered
Filterability increases with temperature. All other things being equal, filtration rates are higher when the product is hot than when it is cold.During filtration, an abnormal rise in temperature in the circulation loop (of more than 4 to 5°C) indicates significant clogging of the membranes. It is therefore advisable to stop filtration and carry out a chemical rinse or cleaning.
Length of filtration cycle and frequency of cleaning
Short filtration cycles (a few hours) enable high filtration rates to be achieved. These short cycles also have the advantage of limiting irreversible clogging, but greatly increase water and cleaning product consumption.Conversely, longer filtration times (24 hours or more) provide a solution to the relatively low flow rates per unit area of tangential filters. The concept of time available for filtration is then more important than that of instantaneous flow rates, with the filter operating automatically, even at night.
Increasing the frequency of chemical cleaning can also increase the flow rate of a filtration system. However, this solution is not recommended as, depending on the configuration, it can reduce the life of the membranes and increase the volume and polluting nature of the effluent.
Rinsing and cleaning operations
The water used for rinsing and cleaning must not contain any substances likely to clog the membranes or react with the cleaning products. As a general rule, it should be pre-filtered on a 1µm membrane. A softener may be necessary.Membrane regeneration is favoured by the action of temperature, hence the need for hot water. For organic membranes, the maximum operating temperatures depend on their composition. Ceramic membranes are sensitive to thermal shock.
The frequency of chemical cleaning must be optimised, as this operation takes a long time (2 to 4 hours), and generates high consumption of water and chemicals. The service life of the membranes also depends on the number of chemical cleanings carried out.
Special conditions of use
Bonding products and inputs
Certain products used for fining or treating wines can have a significant clogging effect. Particular care must be taken when treating with bentonite or using carbon. As the risk of damage depends on the characteristics of the oenological products used and the design of the membranes, it is essential to follow the recommendations of the filter manufacturers.Combining centrifugation and crossflow microfiltration
Centrifuging the products before filtration can increase filtration rates and protect the membranes.Combining microfiltration and tartaric stabilisation
The combination of crossflow microfiltration and electrodialysis treatment enables limpidity, microbiological stability and tartaric stabilisation to be achieved in a single operation. Crossflow microfiltration can also be positioned upstream or downstream of a tartaric stabilisation treatment using cold temperatures. In the latter case, the scale crystals must be separated upstream of the filters (hydrocyclones or other techniques).Filtration of products 'loaded' with suspended particles (sludge, tank bottoms, retentate)
Filtration of products containing large quantities of suspended particles, such as musts from heat treatment, must, lees, centrifugation sludge and retentate, requires specific equipment.Performance averages
Productivity
The flow rates, expressed in L.h-1.m-2, mentioned in the table below, can vary greatly depending on the products to be filtered, the conditions of use and the equipment.The filterability of white and rosé wines is generally higher than that of red wines, certainly due to their lower polyphenol content.
Red wines produced by heating the harvest are generally more difficult to filter.
Type of product | Average flow densities (in L/h.m²) |
---|---|
Must, lees | 20 - 40 |
Red wines | 30 - 60 |
White and rosé wines | 40 - 80 |
Thanks to self sufficiency, the filters can be operated unattended, autonomously, over long periods.
Clarification levels
After cross-flow filtration, the turbidity of wines is generally less than 1 NTU, which corresponds to brilliant wines.For musts, must and lees, turbidities are generally between 0.5 and 5 NTU.
Microbiological stabilisation
The use of tangential filters can help to obtain wines that are low in germs, whatever the initial micro-organism population levels.The retention of yeasts (and in particular brettanomyces) is "total". Depending on the design of the equipment (average pore diameter, hydraulic configuration), some bacteria may or may not remain at the filter outlet.