Sprayer
Vineyard sprayers are made up of several essential components, such as the tank, pump and nozzles, and can be mounted, semi-mounted or trailed. Pressure regulation and filtration are crucial for effective spraying, while pumps and ventilation systems play a key role in distributing the spray mixture evenly.
Precise adjustment at the start of the season and good maintenance of the sprayer are essential for satisfactory spray quality.
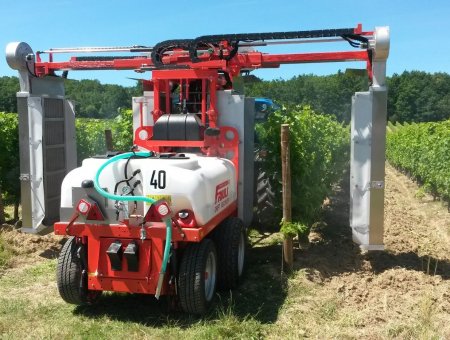
What is spraying?
Spraying consists of spreading a liquid in the form of droplets, the size of which is adapted to the work objectives. The smaller the droplet size, the greater the coverage. The risk of droplet drift and/or evaporation also increases with droplet fineness.Vineyard spraying differs greatly from field crop spraying, partly because of the diversity of vineyard management methods, but also because of the different objectives of the work to be carried out. The main tasks are
- Wood treatments outside the vegetative period (now virtually non-existent since the ban on sodium arsenite in November 2001)
- Cover treatments
- Localised treatments in the fruit-bearing zone

Spraying technologies
There are three main spraying technologies used in viticulture:- the projected jet (mainly used for weed control),
- airblast
- pneumatic (both used for general coverage treatments).
In chronological order of progression of the liquid in the sprayer, we find :
- The tank
- The filter (suction)
- The pump
- The regulator
- Distributor(s)
- Boom sections
- Filter(s)
- Nozzles or pellets
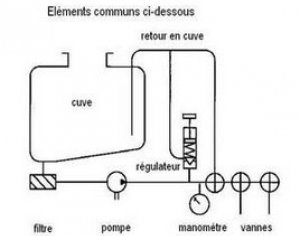
Common sprayer components
Components of a sprayer
Chassis, tank and axle
The chassis
Generally of welded design, the chassis of a vineyard sprayer is made up of a "U" or "tube" section. The U-section offers a number of advantages, in particular resistance to corrosionWhen the chassis is made up of a "tube" section, it is important to ensure that the ends of the chassis are sealed to prevent internal corrosion.
The coupling system
There are 3 main types of hitch.- Mounted
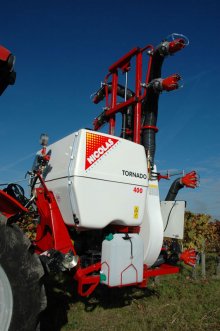
Mounted sprayer (on the 3-point linkage) - Nicolas
- Semi-mounted
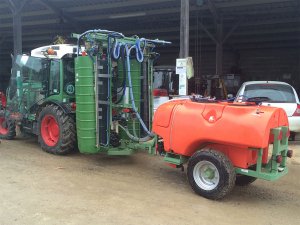
- Trailed
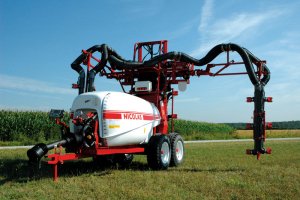
Trailed sprayer (hitch) - Nicolas
The tanks
The main tank is the spray liquid reservoir. A second tank contains the water needed to rinse the circuits and dilute the tank contents. Finally, a third tank is used for rinsing hands and/or nozzles.They are generally made of polyethylene or laminated polyester , but you can also find 'home-made' tanks in stainless steel, mainly on high-clearance tractors when you're looking for a 'made-to-measure' solution.
Materials | Advantages | Limitations |
---|---|---|
polyethylene | ▪ Easy to clean ▪ Resistant |
▪ Difficult to repair |
polyester laminate | ▪ Easy to repair | ▪ Internal roughness makes cleaning difficult ▪ Sensitive to shock and vibration |
Tanks generally have a capacity of between 300 and 2000 litres.
When we talk about vat volume, we need to distinguish between nominal, total, dilutable residual and total residual volume.
Nominal tank volume
maximum capacity of the vat.
Total tank volume
nominal volume + 5% safety volume
Dilutable residual volume
volume of liquid remaining in the bottom of the tank after the pump has been de-primed + in the tank return circuit + in the compensated returns + in the filters + in the agitation system + in the pipes of any product incorporation tank.
Total residual volume
dilutable residual volume + volume of spray liquid remaining in the pipes from the tank to the diffusers.
+ The volume of the rinsing tank must be at least equal to 10% of the volume of the main tank.
The axle
There are three types of axle on the market:- Single axle
- Double axle
- Bogie axle
The choice of axle type is based on various objectives:
- volume to be loaded
- stability required during treatments
- limiting soil compaction.
Double or bogie axles offer good stability during spraying operations, limiting pressure on the ground and, consequently, soil compaction. On the other hand, they have the disadvantage of reducing the turning radius.
The pumps
These are the heart of the sprayer. The pumps move the liquid not only for spraying but also for agitation in the tank. They are characterised by a characteristic curve that represents the pump's ability to move the spray liquid as a function of the required pressure.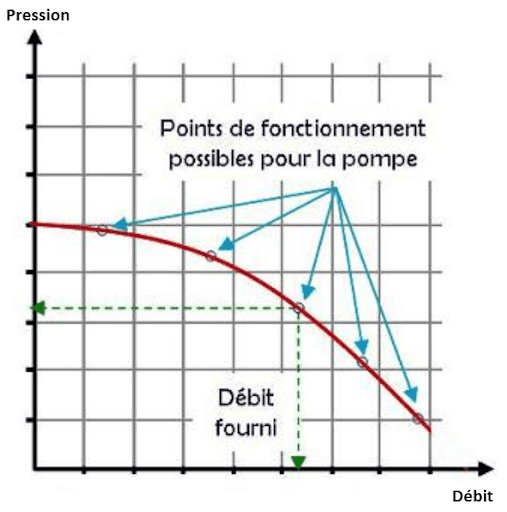
CAUTION: a pump rated at 60 litres per minute (often at a PTO speed of 600 rpm) will only deliver this flow rate at atmospheric pressure. An increase in working pressure causes a reduction in flow, which can be very significant. Centrifugal pumps are the most sensitive to this phenomenon, while piston pumps are the least sensitive.
Although there are a few centrifugal pumps, the vast majority of pumps used are of the piston-diaphragm type.
There are several types of pump on the market:
- Centrifugal pumps
How a centrifugal pump works:
The liquid is drawn in at the impeller shaft. The liquid flows through the impeller at high speed. The centrifugal force sends the liquid towards the discharge, causing it to acquire kinetic energy, which is converted into pressure.
- Piston pumps
How a piston pump works:
The piston moves in a straight line with a reciprocating motion in order to pressurise the liquid. A suction valve and a delivery valve allow the liquid to enter and leave the pump. To regulate the flow, the pump is fitted with an air bell to smooth out the pressure (clipping low and high pressures).
- Piston diaphragm pumps
How a piston diaphragm pump works:
The piston is framed by two diaphragms. The reciprocating movement of this piston is in phase with the suction or discharge diaphragms. A suction valve and a discharge valve allow the spray liquid to enter and exit the pump. Like piston pumps, they are generally combined with an air bell.
The air bell
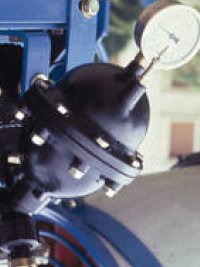
Air bell
The internal pressure is determined by the working pressure. Generally, it varies between ½ (for "low" pressures) and 1/3 (for "high" pressures) of the working pressure.
Filters
- the first filter (sieve) is located at the manhole. It is used to retain coarse elements such as lumps formed during poor preparation of the spray liquid
- a filter protecting the pump, located between the tank and the pump
- the second level of filtration is located between the pump and the control system. This level of filtration is optional.
- a third level of filtration is positioned after the section cut-off valves and the nozzles
- finally, a last level can be positioned just before the diffusers (nozzle filter)
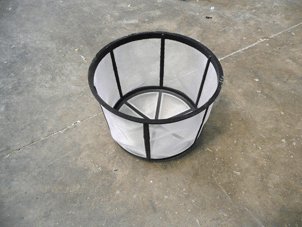
Sprayer filling sieve
- intake filter: 32 to 50 mesh
- section filter: 50 to 80 mesh
- nozzle filter: 80 to 100 mesh
As a reminder:
The filtration capacity of the last filtration levels must be adapted according to the risk of clogging the nozzles and the recommendations given by the suppliers.
It is possible to adjust the filtration fineness but also the volume of the filtration bowl if the filters become clogged.
- Filtration that is too loose can lead to clogged nozzles!
- Filtration that is too tight can lead to clogged filters!
There is an international colour code (which is generally respected) for identifying the filter's filtration capacity.
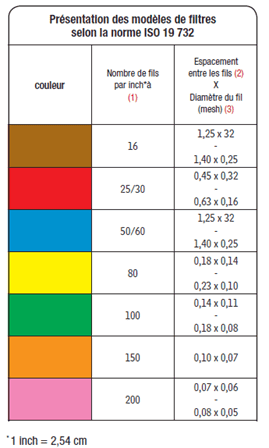
MESH correspondence table
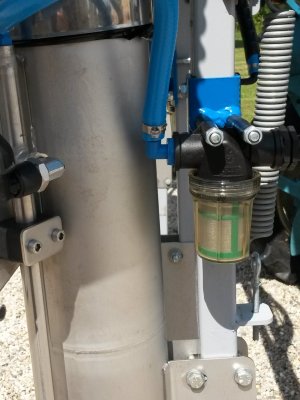
Regulation
The regulator
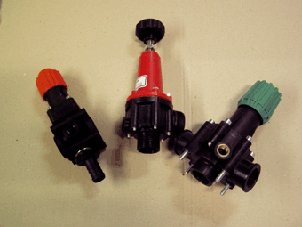
Sprayer regulators
- Constant pressure regulation.
- Calibrated return flow regulation (also known as DPM: flow proportional to engine speed).
Constant pressure regulation
The regulator consists of a variable-load spring (by-pass) which, by modifying the pressure on the spring, which acts on the valve, makes it possible to obtain the desired pressure in the spray circuit. Part of the pump flow is diverted and returned to the tank. The quality of the regulator spring is of vital importance. It must be adapted to the working pressure.
Calibrated return flow control
Regulation is achieved here by diverting part of the pump flow back into the tank, either via an orifice whose cross-sectional area can be varied continuously, giving infinite possibilities for adjustment. Or via multi-calibration adjustment knobs.
The major advantage of this type of regulation is that the flow rate is virtually proportional to the forward speed at a given gear and within a range of 150 revs of PTO speed (450 to 600 rpm).
DPAE
These systems regulate the flow rate according to the forward speed in order to maintain the same volume/ha. these are consoles connected to a pressure sensor and/or flow meter and a speed sensor (GPS or sensor positioned on the wheel). The system regulates the pressure according to the volume/ha chosen in relation to the tractor's forward speed, once the working width has been set in the system. These consoles can also be used to control the opening/closing of sections, and to display and adjust the various spraying parameters (flow rate, pressure, volume/ha, etc.). Beware, some of the parameters displayed on the console are sometimes (often) calculated and not measured, giving the user the illusion of precision/reactivity that they cannot possibly achieve!Distributors or valves
A sprayer is generally fitted with a general cut-off valve and valves for each boom section.
For safety reasons (no spray liquid in the cab), manually-operated spool valves are not permitted in closed cabs. They are replaced by solenoid valves or motorised valves. Motorised valves are preferred to solenoid valves for reasons of reliability and maintenance, although solenoid valves have the advantage of closing almost instantaneously.
A motorised valve can take up to 1 second to close. Both closing devices must be adapted to the operating pressures in the circuit, otherwise they will deteriorate rapidly. Adjustable compensated return valves enable a stable pressure to be maintained when a boom section is closed.
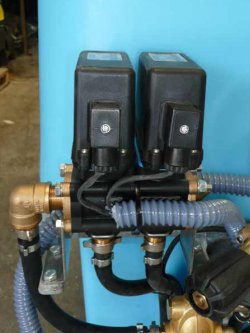
Sprayer distributors
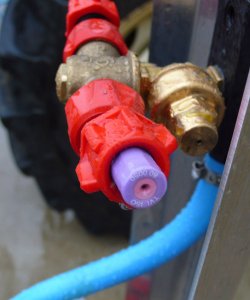
Nozzles holer
Booms
These support the nozzle holders or nozzles, the number of which varies according to the equipment. Their configuration varies considerably depending on the type of equipment.Nozzle holders
These support the nozzle or the pellet, and are generally fitted with anti-drip devices that stop spraying when a valve is closed.
The opening pressure of the anti-drip devices is around 0.3 to 0.8 bar.
The pressure gauge
For sprayers fitted with a digital pressure gauge, it is recommended to fit the sprayer with a needle pressure gauge, which will make it easier to check the information given and detect a problem.
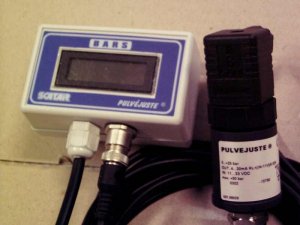
Digital pressure gauge
Two types of pressure gauge are used:
- Bourdon tube devices, which use the deformation of a bent brass tube to move the needle and indicate the pressure.
- Electronic gauges use a strain gauge to measure the pressure and a digital display.
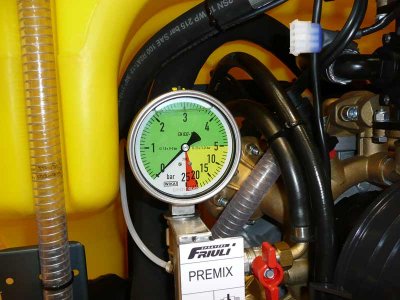
Needle pressure gauges
Expanded scale pressure gauges give good accuracy at low pressures, with a reading over 2/3 of the needle's travel; the last third allows high pressures to be reached with poor accuracy, but with protection for the mechanism (see illustration).
Needle pressure gauges are not allowed in the cab, but they can be placed outside the cab, behind the cab window and within sight of the driver.
Ventilation
Air flow is a very important parameter for successful spraying. For pneumatic sprayers only, air speed breaks up the stream of liquid (spray solution) into droplets and also plays a role in mixing the leaves and penetrating the product into the vegetation.In air-blast sprayers, the main function of the air flow is to carry the droplets towards the vegetation, stirring it so that the spray mixture is evenly distributed throughout the canopy.
The air flow is generated by one or more fans.
Settings and uses
There is no standard setting for all types of sprayer. However, the calculation formulas remain the same.
Adjustment formula
Formula for calculating the volume of spray mixture applied per hectare:
V (km/h) x L (m)
- Volume: quantity of spray mixture to be applied in litres per hectare
- Flow rate: total sprayer flow rate in litres per minute
- V: working speed in km/hour
- L: working width in metres (the distance between 2 passes of the tractor)
Here's how it works
Number of rows treated per pass: 4 complete rows planted at 2 metres apart
Width between rows: 2 m.
Total flow rate of sprayer: 12 L/min
Working speed: 5 km/h.
The volume of spray liquid per hectare planted will be :
Vol (L/ha) = (600 x 12) : (5 x 8) = 180 L/ha
Measuring flow through nozzles
Measuring total flow
In this specific case, where the previous method is not applicable, the total flow measurement, which is faster but less accurate, can be used.
Procedure
- Fill the spray tank to the brim.
- Switch on the sprayer while the hose that fills it continues to flow, causing the liquid to overflow the tank. This operation primes the sprayer circuits perfectly.
- Remove the hose and let the sprayer run for 5 minutes.
- Fill the sprayer with a graduated container until it is completely full again.
The flow rate (expressed in litres per minute) will be equal to the volume of water required for readjustment divided by 5, as the flow rate was measured over 5 minutes (to limit errors).

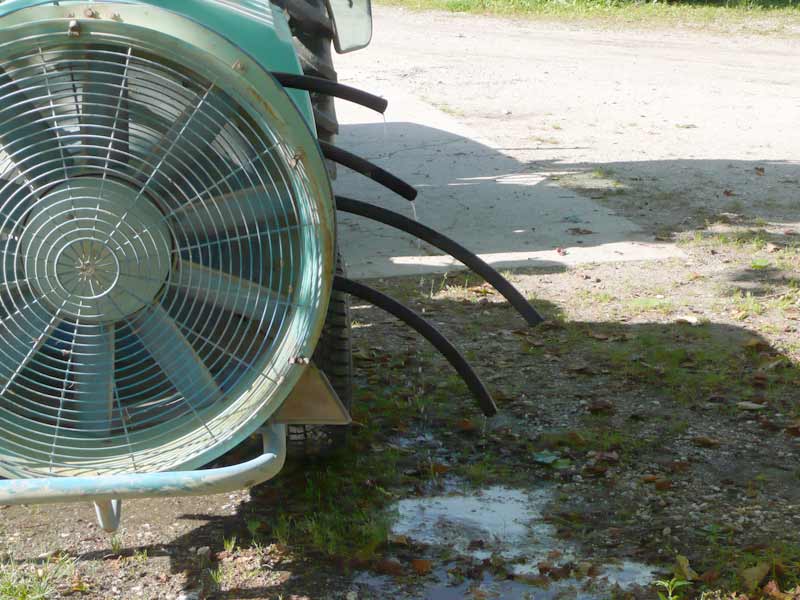
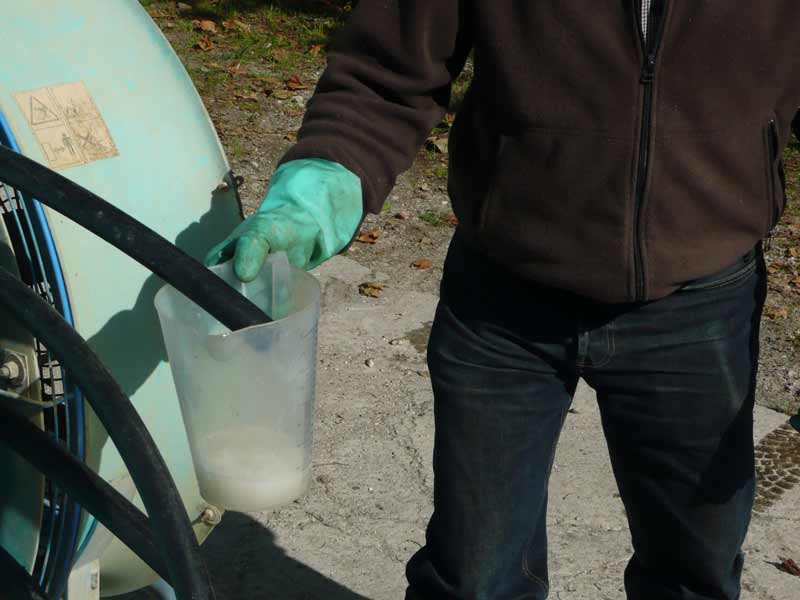
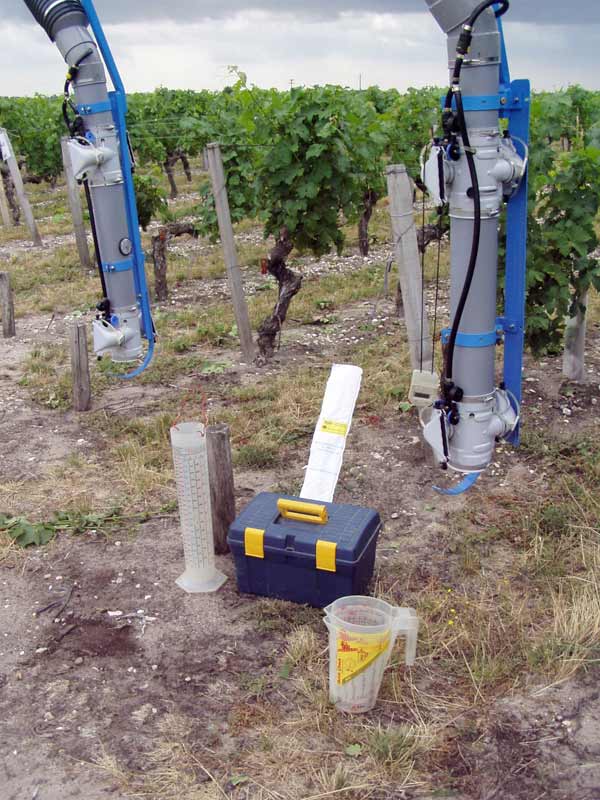
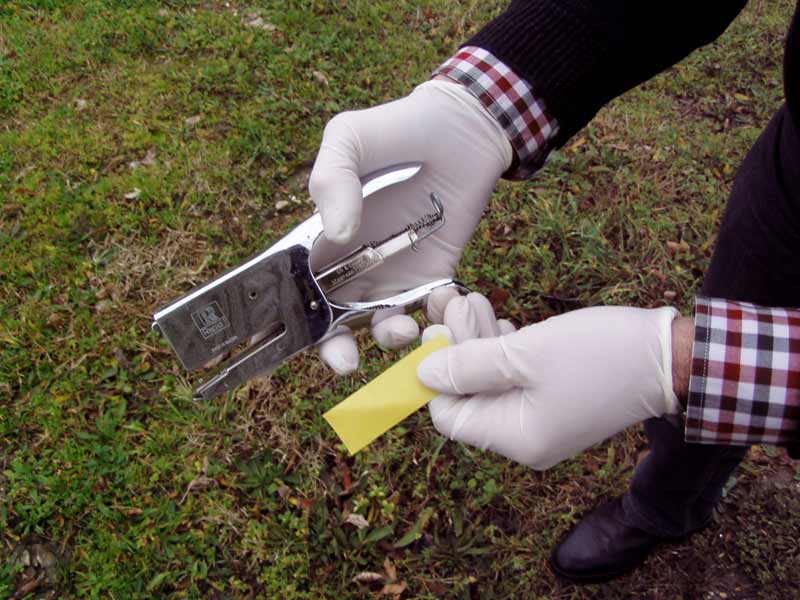
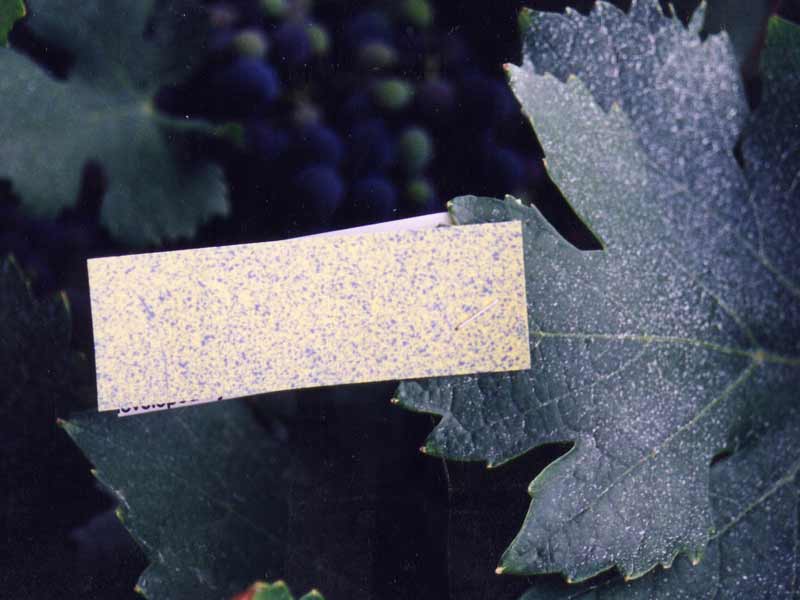
Adjusting an air-assisted sprayer
Example
The accuracy of the PTO speed sensor is checked using a tachometer at the PTO.
The combination of a gearbox ratio enabling the desired forward speed to be obtained at a PTO speed of 540 rpm is determined.
Generally speaking, spray quality tends to deteriorate with increasing forward speed. The choice of speed is therefore a compromise between work rate and application quality.
Generally between 5 and 7 km/h, the choice of forward speed should take into account the following factors, among others:
- the technology used (tyres are often more sensitive to increases in forward speed)
- the volume of air displaced (the greater the volume, the less impact an increase in forward speed will have)
- the distance between the diffuser and the foliage
- the state of the ground in the treated plots (uneven ground -> risk of boom swing)
Preferential spray circuit
It's a hydraulic circuit that offers less resistance than another and on which the liquid flow will be directed. It leads to heterogeneous flow rates between the nozzles or the fingers of the same nozzle.
What causes a circuit to have preferential liquid flow?
- different discharge heads.
- different pressure drops (circuit length, pipe diameter, presence of bends or crushing of the pipe)
Technical and economic selection criteria
Selection criteria
- power available at the power take-off
- oil flow available, if required
- tractor balance for mounted sprayers
- width of plantation
- height of foliage
- thickness of foliage
- topography
- in the open
- localised
adjustment options
purchase price and work rate
When it comes to spraying, we can really talk about targets that need to be reached. Appropriate means will have to be implemented to reach them while respecting the environment.
Clearly, the success of a treatment is the result of a synergy between knowledge of the disease or pest, control processes and a good application technique.
Particular points to watch out for
Vessel shape:
The presence of a diamond tip effectively limits tank bottoms.
Tank gauge:
A dry gauge (no contact with the spray liquid) will remain legible from a distance after several years. Its visibility from the cab is obviously a plus.
Rinsing tank:
Legally, it must have a capacity greater than or equal to 10% of the volume of the main tank.
Hand-wash tank :
Present and easily accessible.
Pressure gauge :
Suitable for the working pressure. Positioned so as to be easily seen by the tractor driver.
Drip guard :
Present.
Filters :
Number and ease of cleaning, respect for graduation.
Diffuser adjustment:
Being able to give them a vertical angle (inclination) and/or a horizontal angle (orientation) is often an important point for improving plant coverage.
Regulations and the environment
Machine design: Operator safety
This directive lays down design rules to meet operator safety requirements.
This directive lays down the design and construction rules to meet the essential health and safety requirements for the operator. The Machinery Directive (2006/42/EC) will be replaced by Machinery Regulation 2023 (1230), which was published on 29 June 2023 but will not come into force until 20 January 2027.
Machine design: Environment
The main requirements are
- Accuracy of application and prevention of drift
- Ease of maintenance and cleaning
- Easy connection of measuring devices such as pressure sensors and flow meters (particularly for technical inspection)
Technical inspection of sprayers
During the technical inspection of the sprayer, a number of points are checked:
- The general condition of the equipment
- The presence of safety devices
- The condition of the plugs and the operation of the filling and emptying systems, etc
- Condition of pipes, hoses, circuits, etc
- Proper operation of measuring instruments: pressure gauges, etc
- Condition of filters
- Flow rates of nozzles, pellets, etc
ZNT in the vicinity of watercourses
By default, a ZNT is 5m; it may be extended to 20 or 50 m depending on the plant protection product's marketing authorisation. Source: DRAAF Nouvelle Aquitaine.
It is possible to benefit from reductions in the ZNT under certain conditions:
1. Presence of a permanent vegetation cover at least 5 metres wide at the edge of water points:
- shrubby for tall crops (arboriculture, viticulture, hops and tall ornamental crops), the height of the hedge must be at least equivalent to that of the crop
- herbaceous or shrubby for other crops
These means must appear on a list published in the Official Bulletin of the Ministry of Agriculture. Each method selected must make it possible to reduce the risk to aquatic environments by at least a factor of three compared with the normal conditions under which the products are applied.
The list of equipment can be downloaded from
info.agriculture.gouv.fr/gedei/site/bo-agri/instruction-2023-282
DSR and DSPPR (Riparian distances)
The result is a set of regulations governing the use of plant protection products in the vicinity of local residents and bystanders.
Safety distances for phytopharmaceutical treatments near dwellings | Ministry of Agriculture and Food Sovereignty
These distances can be reduced by using certain equipment on an official list.
New technologies & spraying
Although not yet fully developed in the field of spraying, new technologies are slowly appearing to facilitate treatment and/or traceability work. These are usually sensors/actuators linked to GPS. They can be used to modulate the dose on an intra-parcel scale and/or automatically cut off sections at the end of the row (which is particularly useful in the case of narrow vines where the rows are not all the same length).
PWM nozzles may provide new technical solutions for taking another step towards precision spraying, but their high cost is likely to penalise any commercial development in viticulture.
Finally, traceability tools (keyfield, etc.) have also appeared in an attempt to automate and simplify the recording of agricultural work and spraying in particular.
Other tools have also been developed to provide easy access to past and/or forecast weather data (weather stations, spatial data, etc.). They are often combined with models or Decision Support Tools
(https://decitrait.vignevin-epicure.com/login) to help the winegrower/advisor position treatments more effectively and choose the right product dose. Some allow simplified traceability of treatment operations.
Quality of spraying
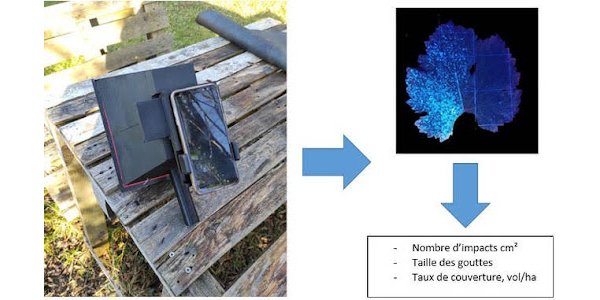
Eval'Pulvé project
The aim of the project (funded by the Nouvelle Aquitaine Region) is to develop a tool for assessing the quality of spraying. It is being carried out by the Gironde Chamber of Agriculture, CTIFL andIFV as part of the Eval'Pulvé project .
How it works
- The vines are sprayed with a fluorescent tracer supplied by our partner Jean-Louis Talon, which fluoresces even when dry.
- Images are acquired in the field using a smartphone and its acquisition medium, following a sampling plan.
Image analysis and interpretation
- The number of impacts per cm²
- An estimate of the median drop size (vmd)
- An estimate of the coverage rate on the leaf and the volume/ha
- The data is processed retrospectively by computer.
The final objective is to develop an application that will enable users to self-assess the quality of their application and provide recommendations on settings.
Recuperator panels
In addition to the spraying technology used, some equipment is equipped with recuperator panels.Historically used for winter treatments with sodium arsenite, sprayers with recovery panels had, since the ban on this product in November 2001, returned to the obscurity of sheds. However, new environmental concerns and the ECOPHYTO plan have given them a second lease of life. While the equipment used for winter treatments with sodium arsenite was simple in design (generally a single panel spray), the use to which they are now put (treatments throughout the season) has seen them evolve considerably, with the addition of a blower in particular. Most of these are fitted with a carrier jet (a droplet production method more suited to recovery), although some pneumatic equipment is fitted with panels. There are various systems for recovering the spray liquid from the bottom of the panels. These generally involve a dedicated piston pump, but peristaltic pumps or hydro-injectors are not uncommon. While they can save around 30% of spray mixture over an entire campaign, they have a number of drawbacks (cost, space requirements, work rate, etc.) which have considerably limited their use. The Cognac vineyards (wide vines, moderate slopes) have by far the highest proportion of sprayers fitted with panels.
Most manufacturers now include at least one piece of equipment fitted with recovery panels in their range.
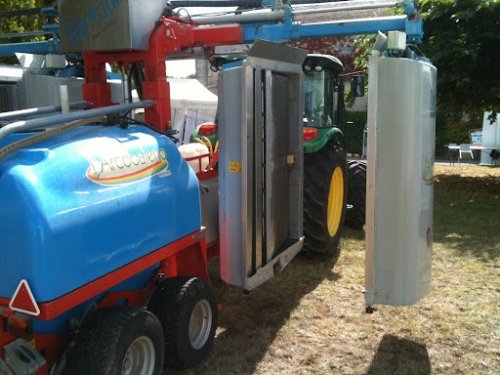
Bertoni sprayer (Arcobaleno) - Photo credit IFV (Davy)
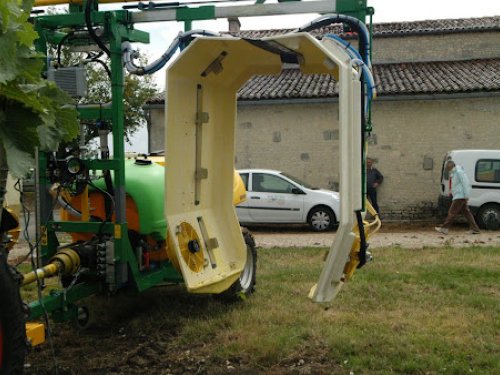
Dagnaud sprayer (Turbipano) - Photo credit IFV (Davy)
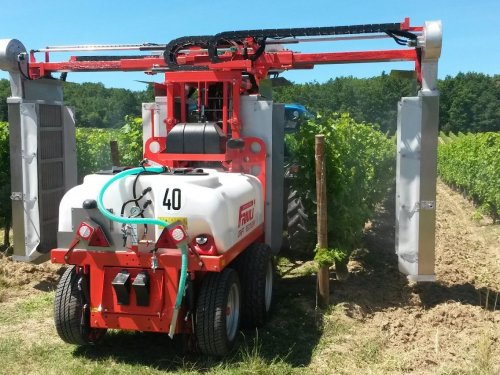
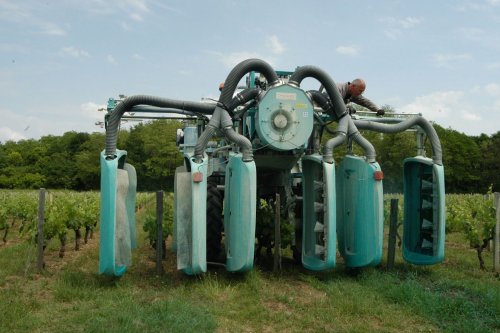
- Choice of spraying techniques for winegrowing, the PERFORMANCE PULVE tool - 2022
- Vititunnel, an automatic system for covering vines to combat mildew - 2021
- Checking spray quality tutorial - 2020
- [EQUIPMENT TEST] Adjustment sheet: water-sensitive paper, how does it work? - 2020
- [EQUIPMENT TEST] Set-up sheet: black plates, how does it work? - 2020
- Order of introduction of plant protection products when mixing - 2020
- Sprayer wintering procedure summary sheet - 2019
- The 10 golden rules of vineyard protection - 2019
- PulvEco, a new online tool to assess the quality of spraying on wide vines - 2019
- How to optimise the use of recovery panel sprayers? - 2018
- Powder assessment - 2017
- Order of 4 May 2017, Placing on the market and use of plant protection products - 2017
- Evaluation of the effectiveness of drift nets - 2017
- Practical guide to setting up and using vineyard sprayers - 2017
- Optimising sprayer performance - 2016
- Checking spray quality tutorial - 2016
- Sprayer settings and equipment selection conference - 2016
- The benefits of supporting winegrowers in adjusting their sprayers - 2015
- Test results for recovery panels - 2014
- [EQUIPMENT TEST] Comparative test bench, sprayers with recovery panels - 2013
- Optipulvé: a tool for optimising application rates in narrow vineyards - 2013
- Direct injection of plant protection products in vineyards - 2011
- Checking your sprayer - 2011
- [EQUIPMENT TEST] Comparative test bench, drift reduction in viticulture - 2011
- [EQUIPMENT TEST] Comparative test bench, spraying wide vines - 2011
- Technical meetings on crop protection spraying - 2010
- [EQUIPMENT TEST] Comparative test bench, spraying wide vines - 2009
- All you need to know about storing plant protection products - 2008
- Which equipment for confined spraying - 2008
- Preparing sprays and managing phytosanitary effluents - 2007
- How can we improve spraying? - 2003