Hygiene equipment
Hygiene in a winery is essential to prevent microbial contamination that can spoil the wine. It is crucial to put in place rigorous procedures to ensure the cleanliness of winemaking and storage equipment. Cleaning eliminates visible contamination, while disinfection neutralises residual micro-organisms.
By adapting cleaning techniques to the different materials and types of contamination, a structured hygiene plan ensures optimum quality wine production.
By adapting cleaning techniques to the different materials and types of contamination, a structured hygiene plan ensures optimum quality wine production.
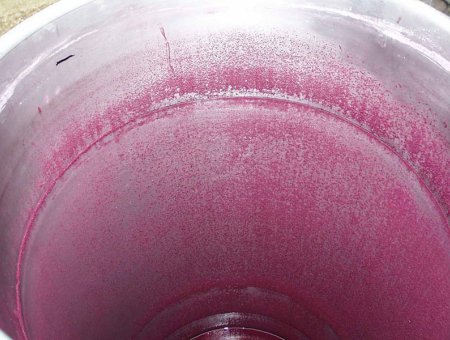
Introduction to cellar hygiene
The winery - whether for vinification or storage - and all the equipment in contact with the grapes, must or wine, are ideal surfaces for micro-organism contamination, the main sources of spoilage in wines, before or after packaging.All these surfaces need to be treated with the utmost care, which means implementing hygiene procedures. A distinction is made between cleaning and disinfecting procedures.
Cleaning a tank means obtaining a healthy container, i.e. one that is completely free of limescale, correctly cleaned and carefully disinfected.
Descaling, like any cleaning operation, involves 4 stages: wetting (the detergent comes into contact with the soil and establishes a bond greater than that existing between the substrate and the soil), displacement of the soil (the detergent composition adsorbs to the substrate, coating the soil, which can then detach by forming aggregates), keeping the soil away from the surface to be cleaned (dispersion of the soil and separation in the detergent solution by mechanical action and turbulent circulation), and finally, removing the soil by rinsing.
The difference in roughness (high roughness: cement, wood / low roughness: stainless steel, epoxy resin) explains the difference in procedures, which are simpler and easier depending on the type of coating. This is an important factor, as are the notions of accessibility, ageing and cleanability of different equipment (open surfaces, closed circuits, etc.).
The active ingredient used in the cleaning solution will be adapted to the stain.
It must respect the substrate and the nature of the materials used.
It must respect the substrate and the nature of the materials used.
Organic stains are linked to the product and endogenous residues brought by the grape juice, must or wine, such as colouring matters, tannins, tartars and sugars, with the common denominator being the low pH (between 3.5 and 4) of these residues.
On the other hand, the mineral salts (mainly calcium and magnesium) brought in by the water used in the various processes will produce residues such as mineral tartar or limescale, which will tend to have a high pH (between 9 and 10).
In chemistry, a basic principle is applied to eliminate stains according to their classification on the pH scale:
- to remove organic stains with an acid pH, use an alkaline product
- to remove mineral stains with an alkaline pH, use an acid product
The aim of the cleaning operation is to remove soiling that is visible or adheres to a surface. It consists of loosening the stain before dissolving it. Most of the time, water alone is not sufficiently wetting, in the chemical sense, and does not have sufficient properties to eliminate soiling.
- The combined use of heat and/or pressure (mechanical effect) can achieve more effective cleaning.
- The use of a detergent is often necessary to break the surface tension and adhesion forces that have built up between the substrate and the stain (force expressed in Newtons/metre).
Nitric acid is used to remove mineral salts or to passivate stainless steel surfaces (wine circuit interiors or vat walls) in order to restore shine to the surfaces
To remove a layer of vinegar scale from the walls of a vat, we use a solution of alkaline detergent and a closed circuit process for a certain period of time, until the scale is completely dissolved.
In addition to the active ingredient (basic molecule), the main components of a cleaning product are as follows
- Surfactants (chemical action),
- Sequestering agents (calcium and magnesium traps),
- Scale and corrosion inhibitor,
- Oxidising agent (elimination of colouring matter),
- Associated disinfectant (in the case of a disinfectant detergent).
The purpose of disinfection is to eliminate the micro-organisms that remain on surfaces after cleaning. The general mode of action of a disinfectant product is to bind its active principle to the cell wall, then denature and destroy the cytoplasmic membrane proteins or oxidise the membrane constituents.
This leads to perforation and blockage of the microorganism's metabolism, with lethal consequences.
Disinfection is an operation with a temporary effect : the risk of contamination reappears depending on the environmental conditions in the winery (draughts, fermenting vats).
This is why it is advisable to disinfect a surface as soon as possible after using the equipment.
This is why it is advisable to disinfect a surface as soon as possible after using the equipment.
Chlorine is the oxidising active ingredient that has long been used, for its many advantages (detergent, disinfectant, deoiling and deodorising action). It was banned around 25 years ago, only to be recognised as a precursor factor in the formation of TCAs (TriChloroAnisols), which give wines their famous corky taste.
A wine stored in a vat could have this taste without coming into contact with a cork!
To put things into context, chlorine is not currently banned (it is widely used in other sectors of the food industry).
It should also be noted that when setting up a chlorine-free hygiene plan on a production site, the supply and composition of the water used for cleaning and rinsing must of course be taken into account, and it must be ensured that it does not contain any chlorine contamination...
Peracetic acid is being used more and more, as it is highly effective in rapidly killing a range of micro-organisms. Quaternary ammoniums and amines are used on an anecdotal basis.
Floors and walls are carriers of organisms and vectors of the risks of deterioration, as is the presence of stagnant water. Keeping them clean and draining away water is desirable.
Implementing cleaning and disinfection
The inventory of equipment, surfaces and risks associated with each production operation leads to the implementation of hygiene procedures. These procedures must be adapted to the nature of the material and its surface condition, the geometry of the equipment and the nature of the contamination: the concept of GOOD SENSE. They must take into account the most appropriate means available: the concept of working with TACT.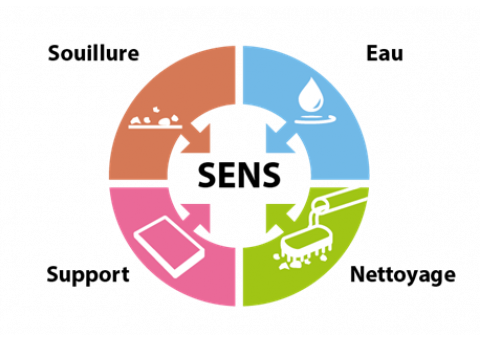
Good SENSE principle
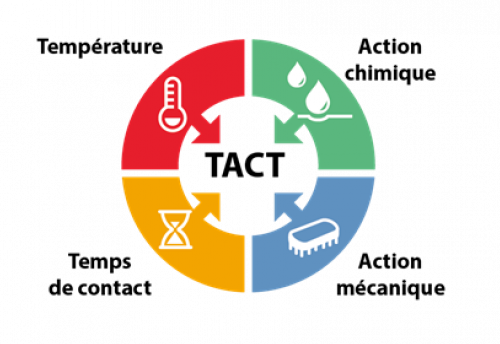
The hygiene plan
The hygiene plan is the culmination of the implementation of cleaning and disinfection procedures. It can be summarised in 8 steps:- Study the water supply (where? flow rate? pressure? quality?)
- Make an inventory of the facilities to be treated
- List the types of materials used (corrosion)
- Choose the cleaning and/or disinfection processes
- Determine the equipment required (frequency of use, duration, feasibility of installation)
- Define control methods
- Ensure the safety of operators
- Ensure proper respect for the environment
- Who (number and skills of staff required for cleaning and disinfection operations)?
- When (when, after what use, how often)
- How should it be done?
- What equipment should be used (manual, mechanical)?
- Which products? How long?
Special case of cleaning: descaling
General information on descaling
The descaling operation
For most wineries, whatever efforts are made to recover bitartrate in the form of crystals, chemical descaling remains essential. It is the first cleaning operation.It is advisable to descale empty tanks before the harvest period, and to descale tanks - in particular - after each racking, to prevent the layer from consolidating and becoming a source of contamination for the wine or equipment and increasing the risk of microbial spoilage. Don't forget to free concrete vats (2% tartaric acid) after descaling.
Descaling does not only concern the vat room. Pipes and taps, heat exchangers, filters and harvesting, transport and processing equipment are all surfaces where scale crystals can settle and accumulate. As well as causing malfunctions, this contamination encourages the growth of mould.
Tartar crystals can also contribute over time to degradation of the tank wall (depassivation of stainless steel, tarnishing of resins or plastics, disintegration of cement).
Descaling is an essential stage in equipment hygiene. As well as controlling spoilage micro-organisms (contamination of equipment and wine), this operation helps to optimise work in the cellar by controlling energy costs (heat exchangers), staff costs (regular operations) and by improving the efficiency and durability of the equipment (maintenance).
For the vat room and pipework, chemical descaling is carried out in a closed circuit (15 to 40 minutes) or by soaking (a few hours), after a pre-washing stage with cold water, usually in waste water. This is followed by a water rinse to remove any traces of chemical residue.
To avoid denaturing the lining of certain tanks, it is essential to limit the soda concentration to 30g/L .
It is advisable to check the compatibility of such a chemical treatment with each of the materials treated and to adapt a compatible concentration.
To prevent pumps being damaged by residual scale crystals, a buffer tank with a strainer is recommended when setting up a closed circuit for descaling a tank. Any scale-retention device placed upstream of the pump prevents damage.
The success of a descaling operation depends not only on the nature of the substrate and the extent of the scale layer, but also on the descaling solution used (a strong alkaline, often soda-based), its concentration, the length of time it is applied and the equipment used. In the winery, it also appears that descaling in a closed environment has its limits, due to the accessibility of the descaler to the entire surface (cleanability): tasting taps, valves and seals will be correctly descaled if the procedure involves dismantling these elements.
Tartaric acid, tartar
A natural component of grapes and wine,tartaric acid - a fraction - precipitates during the winemaking process - particularly under the influence of lower temperatures and higher alcoholic degrees - in the form of potassium bitartrate crystals.
These tend to cling to the surfaces in contact with the wine under the effect of several phenomena: interfacial tensions, Vander Waal forces and electrostatic forces.
The scale thus formed is a living structure containing micro-organisms that are only waiting for favourable conditions to develop: humidity, temperature and substrates.
These conditions are present as soon as the tank is filled and can lead to spoilage.
These tend to cling to the surfaces in contact with the wine under the effect of several phenomena: interfacial tensions, Vander Waal forces and electrostatic forces.
The scale thus formed is a living structure containing micro-organisms that are only waiting for favourable conditions to develop: humidity, temperature and substrates.
These conditions are present as soon as the tank is filled and can lead to spoilage.
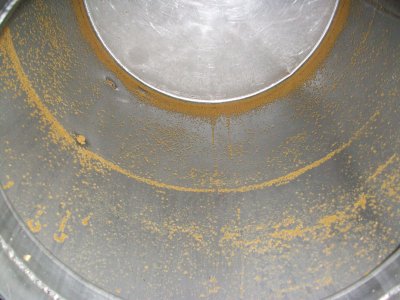
A scaled tank
Descaling is one of the most important steps in cleaning. What's more, you can't effectively disinfect a substrate that isn't perfectly clean. Scale is a stain ; trying to disinfect a scaled surface is utopian and even dangerous, since it will be difficult to rinse it thoroughly.
The descaling detergent
The descaling detergent should loosen, dissolve and disperse adhering scale. Its main action, when the main agent is soda, is based on the solubilisation of potassium bitartrate to form a double tartrate of potassium and sodium.
Its action will be reinforced - to separate the stain from the surface by establishing a greater adhesive force than those existing between the support and the stain - by the presence of surface-active substances (which lower the surface tension of the descaling liquid and interfacial tensions) and/or sequestering and surfactant agents.
Its action will be reinforced - to separate the stain from the surface by establishing a greater adhesive force than those existing between the support and the stain - by the presence of surface-active substances (which lower the surface tension of the descaling liquid and interfacial tensions) and/or sequestering and surfactant agents.
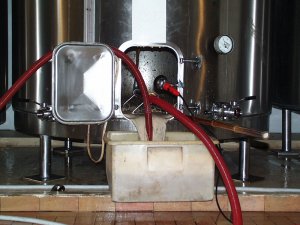
Descaling a stainless steel tank with soda
The soda
Soda destroys limescale crystals by saponification and facilitates its solubilisation and disintegration. In the case of strong alkaline agents designed to descale "open" surfaces - harvesting, transport and treatment of the harvest - such as the grape harvesting machine, reception bins and crates, the presence of a foaming agent means that the descaler can be applied in a static situation. This application uses specific equipment that generally combines compressed air to form an adherent foam: the foam gun.Sodium hypochlorite
Chemically compatible with soda ash and certain surface-active agents, oxidising agents such as sodium hypochlorite can be combined to reinforce detergency through their non-selective oxidising action, which helps to destroy stains that are difficult to remove, or by providing a disinfectant action (in the case of tanks or surfaces that are scaled or mouldy).Pre-washing
Very soon after the wine has been racked, pre-washing with water ensures that some of the crystals attached to the walls of the vat are removed . This process is made all the easier by the rapidity of the wash, the high temperature of the water and the mechanical effect of the cleaning device.Pre-washing therefore helps to significantly reduce the amount of descaling soda. Pre-washing with hot, pressurised water may be enough to avoid chemical descaling. The quantities of pressurised hot water needed for descaling are comparable to the volumes of alkaline solutions used for descaling with soda (on average 2 litres of water per HL of vat room).
The pressure causes the scale to detach, allowing it to be recovered in the wash water and considerably limiting the pollution generated by descaling . This is half as much as when descaling with soda. While this is a physically demanding and time-consuming operation, descaling with pressurised hot water increases the success of the chemical treatment and reduces its polluting power.
If the scale layer is thicker, the quantity of product or its concentration needs to be increased. It is this parameter that will determine the saturation - and effectiveness - of the alkaline solution and its reuse.
The implementation of a descaling operation, whatever the time or surface (open or closed equipment, floors, etc.), must be prepared. Although the concepts of cleanliness and hygiene seem simple at first glance, they need to be understood by the cellar staff. Training is essential; it will emphasise the importance of hygiene and its consequences for the product. It will cover the different phases of descaling - which constitutes the different phases of cleaning, as descaling can be considered as a specific cleaning: pre-washing, chemical descaling, rinsing.
You should be familiar with the different products used (composition, action, dose, safety instructions) and how to use them. Finally, in agreement with all the staff, as part of the general hygiene plan, the operation must answer the following questions:
- What: what equipment needs to be descaled?
- When should it be done? when should it be done? After what use? How often?
- How should it be done? with what application equipment?
Before descaling, the first step is to prepare the surface to be descaled:
- Drain and evacuate the products produced (grapes, musts, wines) by opening pump body drains, inspection hatches, valves, etc..
- Put away (after cleaning) all small items of equipment that may impede staff movement or restrict water drainage: pumps, hoses, buckets, pallets, etc.
- Eliminating scale crystals is a preamble to descaling.
- Remove solid waste using squeegees, brooms and shovels. Carrying away large quantities of solid matter requires a lot of water and clogs up drains and decanters.
- Make the surfaces to be treated as available as possible: destemmer cage or hedgehog, grape harvest conveyor belt, outside or inside surfaces of vats, uncoiling of pipes.
- Set up the equipment: hoses, prepare the pressure washers, foam cannons, pumps, reception tank and strainer (for the closed circuit), sprinkler system (nozzle, jet).
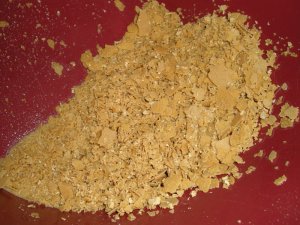
Scale crystals
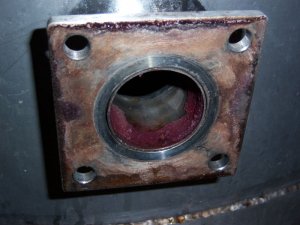
Scaled valve
The aim of the pre-wash phase is to remove as much dirt as possible from the surfaces. It's important to do this as quickly as possible, before the dirt has dried, whether it's inside a press or a freshly drawn-off tank. Water will be the main pre-wash agent, but as we have seen, its action can be reinforced by several means:
- Mechanical : pressure makes it easier to lift off. The maximum pressure to be used is around 25 bar, because beyond this pressure, removal is perfect but the dirt is displaced, or even misted in the air.
- Flow rate : a large volume of water can carry away a lot of dirt
- Soaking or contact: the longer the water and/or foam is in contact with surfaces, the greater its ability to dissolve scale
- Temperature : hot water makes it easier to remove some of the scale.
Descaling
A sprinkler system is used to spray a solution onto the inside walls of the tank. The difficulty of removing the solution is linked to the nature of the material making up the tank wall and its roughness. Observations made in various wineries confirm the ability of materials to cling more or less strongly to scale.Logically, untreated concrete and wooden vats retain the most scale crystals and require the largest volumes of water, and the most pollution.
Type of tank | Adhesion | Resistance to detachment | Volume of water used (1/100 hl) |
Pollution flow (g COD/100 hl) |
---|---|---|---|---|
Raw concrete | High | High | 133 | 1567 |
Wood | Strong | Strong | 107 | 1808 |
Epoxy coating | Strong | Low | 108 | 2394 |
Fibreglass | Medium | Medium | 65 | 1452 |
Stainless steel 2B | Medium | Medium to high | 101 | 1040 |
Electropolished stainless steel | Low | Low | 34 | 672 |
The descaling of cement, glass cement and ceramic vats must be followed by franking, in order to protect the cement from the wine due to the migration of calcium and other compounds. This is generally done with tartaric acid (in a closed circuit) and is followed, after drying (about 24 hours), by a cold water rinse.
Similarly, the passivation layer - degraded by soiling and the chemical descaling operation - must be reformed on the walls of stainless steel tanks.
When descaling solutions are not recycled, they can only be disposed of in accordance with regulations if they have been neutralised.
For "open" surfaces - harvesting, transport and grape processing equipment - the sprinkler system is not suitable. The foaming descaler solution is much more appropriate: the foam adheres to the entire scaled surface and the action time is managed by the final rinse with water, which ends the contact between the chemical formulation and the surface. As a result, the foam gun is becoming increasingly popular in wineries, and can also be used to treat walls, the outside surfaces of vats and floors. Compared with the spraying solution for the vat room, the 'foam' solution has certain limitations, notably the lack of mechanical action. Nevertheless, the results are very satisfactory.
The implementation of a descaling operation, whatever the time or surface (open or closed equipment, floors, etc.), must be prepared. Although the concepts of cleanliness and hygiene seem simple at first glance, they must be understood by the cellar staff. Training is essential; it will emphasise the importance of hygiene and its consequences for the product. It will cover the different phases of descaling - which constitutes the different phases of cleaning, as descaling can be considered as a specific cleaning: pre-washing, chemical descaling, rinsing.
You should be familiar with the different products used (composition, action, dose, safety instructions) and how to use them.
Practical parameters for use
Most chemical descalers are highly caustic (pH of a 1% solution at 20°C > 13) and are obtained froma concentrated mixture of alkaline agents, sequestering agents and surfactants.The recommendations given by the manufacturer (technical data sheet) should be followed very carefully with regard to :
- Compatibility with the nature of the material
- Concentration of use: this will depend on the extent of soiling (thickness of scale) and the nature of the material
- Temperature of use
- Contact time
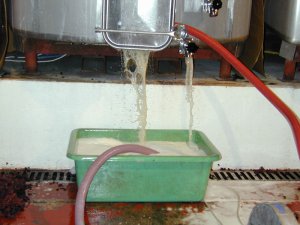
Closed circuit for descaling a tank
The minimum amount of water needed to create a closed circuit (100 to 500 litres) is poured into the tank or recycling tray, and the pump is started (photo 4). In a separate container, the descaling solution is prepared: it is added to the closed circuit gradually to avoid thermal shocks (which accompany dissolution) that could damage the pump or pipes.
The solution is applied in a closed circuit, using nozzles or washing spheres. It is sometimes necessary to move this equipment during the cycle to reach the entire surface of the tank.
The concentration used determines the speed of descaling. The concentrations quoted by the manufacturer are often very broad, and it is often possible to work at the lowest concentrations in the range offered.
Don't overlook the possibility of working at temperatures higher than room temperature, when this is proposed, in order to optimise descaling efficiency or contact time.
The closed circuit is also suitable for descaling filters (diatomaceous earth, drum filters, etc.) after pre-washing. Application times vary from 10 to 90 minutes.
At the end of a closed-circuit descaling cycle, if the tank is completely descaled (visual check), the solution can be used for another tank. If scale remains, the solution is saturated. The operation should then be repeated (do not refill the solution). If you wish to recycle these solutions, and whenever possible, it is essential to saturate them thoroughly. Consult the supplier or service provider offering the recycling service.
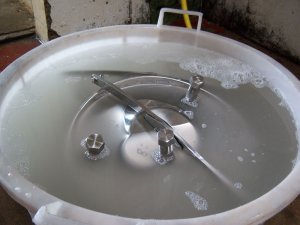
For soaking applications,follow the manufacturer's recommendations. Soaking dismantled parts allows the descaler toact on all their surfaces.
The lack of mechanical action in the case of soaking generally means a longer contact time (up to a few hours), which should be respected.
The lack of mechanical action in the case of soaking generally means a longer contact time (up to a few hours), which should be respected.
When descaling "open" surfaces, the use of a foaming descaler is the most appropriate.
The foam adheres to all horizontal or vertical surfaces. The recommended contact time is generally no more than 60 minutes (the foam will eventually "come off"). The application tools on the market (foam gun, central unit), which do not require a major investment, perform this function correctly, as long as the recommendations are followed.
Rinse well
Any descaling operation ends with a rinse. The water rinse or rinses are carried out when the inspection (usually visual) confirms that the chemical descaling has been successful. In the case of a closed circuit, the rinsing time must be sufficient to eliminate all the basic solution.There are several ways of checking that rinsing is sufficient, either by checking for the absence of chemical residues (phenolphthalein test), or by checking that the pH of the rinsing water has returned to a neutral pH, or more precisely to the pH of the same water leaving the tap.
Phenolphthalein test
Collect approximately 10 cL of water from draining the equipment or surface.
Add a few drops of phenolphthalein. Rinsing the material is correct when no pink discolouration appears.
Collect approximately 10 cL of water from draining the equipment or surface.
Add a few drops of phenolphthalein. Rinsing the material is correct when no pink discolouration appears.
If foam has been applied to a surface, the complete disappearance of the foam indicates that rinsing is complete. However, it is advisable to carry out a test using phenolphthalein or a pH indicator.
Several sequential rinses are more effective than a single continuous rinse, for the same amount of watering time.
Finally, make sure that the water drains from all the parts that have been descaled. Accumulations of residual water (pump casings, low points in pipes) are potential growing media.
they are also potential culture media.
Organic load
The descaling solution represents a significant organic pollution solution, due to the presence of bitartrate and toxic due to the high presence of sodium and a high pH level. The main concern is to reduce the volume of this effluent. To achieve this, the choice of surfaces and materials is well known. Pre-scaling operations (pre-washing, pressure, hot water) optimise the volumes to be treated.Recycling soda solutions is an increasingly common way of significantly reducing effluent discharge. Finally, for safety reasons, operator protection is essential to reduce the risk of accidents.
By virtue of its chemical composition, tartar - or more precisely potassium bitartrate - an organomineral deposit, has the ability to adhere to the materials making up most of the materials and equipment encountered in the wine industry. This adhesive strength is closely linked to the roughness of the substrate.
Descaling tanks and other equipment used to be carried out mechanically, but nowadays it is usually done using soda ash. It is based on the solubilisation of potassium bitartrate to form a double tartrate of potassium and sodium: the seignette salt. The soluble potassium bitartrate is thus eliminated in the descaling solution.
The organic load (pollution load) of descaling effluent is very high. BOD5 (5-day Biological Oxygen Demand: the amount of oxygen required over 5 days by the micro-organisms in the water to oxidise some of the carbonaceous matter) levels in excess of 50,000 mgO2/L are common, as are COD (Chemical Oxygen Demand: the amount of oxygen required by powerful chemical reagents to oxidise the matter in the effluent) levels (often in excess of 100,000 mgO2/L).
Scaling juices are characterised by a high pH, which can upset the balance of a natural environment or biological treatment process. From a practical point of view, staff carrying out descaling often use a constant quantity of soda for each of the tanks, without taking into account the quantity of scale to be eliminated. This explains the wide variation in BOD5 and COD content.
Controlling effluent for the environment
The pollutant load from descaling solutions is very high. It consists mainly of water. The first step in controlling the pollution load will be to improve the management of water flows in the cellar, by :- Limiting the impact of the pollutant load and therefore preserving the quality of the natural environment
- Limiting water consumption
- Reducing water bills
- Reducing downstream effluent management costs (infrastructure, operation, maintenance)
- Optimising the purification of wine effluent
Raising staff awareness is an important factor in reducing water consumption without compromising the quality of descaling. Not leaving a tap on unnecessarily (by using an automatic shut-off spray gun), carrying out dry pre-cleaning, checking installations for hidden or visible leaks - these are all basic ways of saving water. The result is above all linked to the constant concern of management staff to limit wastage. Monitoring consumption is strongly recommended to prevent over-consumption.
Reducing the volume of water and the pollution load also involves optimising the procedure used: nature and concentration of the product, contact time, temperature, importance of the mechanical effect. These parameters have already been presented, and we will just stress the use of hot water for pre-washing, the need to match the sprinkler system to the volume of the tank and the importance of rinsing control.
The use of a foam gun for open surfaces (and vertical parts in particular) is a tool that can significantly reduce the volume of effluent and water used (especially for rinsing).
A significant reduction in the pollution load can be achieved by recovering the descaling solution and recycling the limescale (photo opposite). This method involves using a specially developed descaling solution to dissolve the bitartrate to a significant extent.
From a practical point of view, the concentration of bitartrate in the solution, which is inversely proportional to the dissolution potential, is monitored by density.
The bitartrate is recycled using a method developed by J-P. Faure. In the descaling liquid, the first precipitation in the form of potassium acid tartrate is carried out by acidification (sulphuric acid) of the medium to a pH of 3.56
The solution to be treated is placed in a shaking tank for 1 hour, followed by 12 hours of decantation. The crystals are then recovered and dried. The supernatant, which still contains more than 20 g of tartaric acid, is treated by distillation. The juice is acidified and a calcium carbonate milk is added. This acidification forms calcium sulphate, which is essential for recovering half the tartaric acid not precipitated by the calcium carbonate. The recovered calcium tartar crystals are wrung out and then dried.
This type of recycling and recovery should be preferred for larger wineries. For smaller wineries, recovery is carried out by local or regional collection centres.
Recycling empty packaging from commercial descaling solutions is another way of controlling effluents.
The final important factor influencing the pollution load, through the ability of scale to form and adhere, is the nature of the material. Thus, the extent of scaling depends on the nature of the surface (table 5) and its surface condition.
Material (tank) | Scaling resistance | Resistance to delamination | Impact on pre-wash water | Need for descaling |
---|---|---|---|---|
Rough concrete, wood | Strong | High | High water volume, high pollution flow | Yes (pollutant) |
Epoxy coating | Strong | Strong | High water volume, high pollution flow | No |
2B stainless steel, fibreglass | Medium | Medium to high | Medium water volume and pollution flow | Often (fairly polluting) |
Electropolished stainless steel | Low | Low | Very low water volume and pollution flows | No |
Deposits are lower on B2 stainless steel (commonly used in the industry) and fibreglass tanks, but descaling is often necessary. Epoxy coatings scale easily, but are easy to remove: wash water and flow are important, but descaling is not necessary.
Electropolishing stainless steel greatly reduces scaling: water volumes and pollution flows are very low and descaling is not necessary.
The state of wear of the surfaces must be taken into account when deciding on the procedure to be used.
Stainless steel and descaling
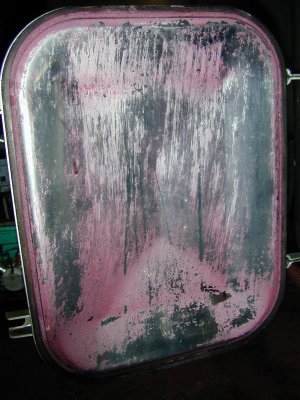
Scaled tank door
Scaling on a stainless steel (inox) surface depends on the type of finish. The pickled cold-rolled bright finish (coded 2B) is the most commonly used. Bright annealing (coded 2RB), which has a lower roughness, limits the adhesion of scale compared with the 2B finish. The electropolished surface has the lowest susceptibility to scaling, but represents a much higher investment, which can be "recouped" in the long term.
The nature of the weld (weld bead) has an impact on the ability to scale: it is greater for a rough weld (whether pickled or not) than for a polished or ground weld.
Lastly, whatever the material, the degree of wear and tear has a considerable impact on the ability to scale. This applies to surfaces (tank walls, vat doors, etc.) as well as seals.
The nature of the weld (weld bead) has an impact on the ability to scale: it is greater for a rough weld (whether pickled or not) than for a polished or ground weld.
Lastly, whatever the material, the degree of wear and tear has a considerable impact on the ability to scale. This applies to surfaces (tank walls, vat doors, etc.) as well as seals.
Safety
Technical data
Decalcifying solutions generally have a very alkaline pH, and it is important to comply with the conditions for use, which are set out in the product data sheet. This sheet, which accompanies each of these dangerous products to the winery, provides information on its main properties and how to use it (concentration, contact time, etc.). It also contains recommendations for handling and storage.Safety data sheet
The safety data sheet, which identifies the supplier, provides information on the components and their hazards. It sets out first aid measures, precautions to be taken, toxic and ecological information and information on the disposal and transport of the product, as required by regulations.Label
In addition to these elements, the label on the packaging confirms the nature of the product, and the pictogram indicates the risks to health and the environment.Personal protection
Protective gloves and goggles must be worn if the product is classified as corrosive, harmful or toxic, which is the case for caustic products. Wearing protective gloves and goggles prevents the product from coming into contact with the skin or splashing into the eyes during use. This avoids burns and potential allergy problems. Use waterproof gloves that are compatible with the use of alkaline products (made of neoprene or nitrile, for example).Risks
Unfortunately, mixing a concentrated caustic with an oxidising product is still one of the most common causes of accidents in the workplace (sudden release of oxygen, heat, splashes).In general
- When diluting, always add water first (to avoid the risk of splashing, foaming, etc.)
- Avoid topping up the level of the new product with a base of the old, out-of-date product (contamination of the new product with risk of deposits,...)
- Always use the product in its original, suitable packaging (do not unpack)
- Never leave unidentified and unlabelled products lying around
- Appoint a specific person to be responsible for supplying products (changing cans); this person will be trained
- Wear safety protection for all handling: gloves and goggles
- Handle pure products close to a water source or safety point
- Do not overdose products
As for storage
- Always store products away from heat, in a ventilated room reserved for this purpose and identified on the site plan, with a register
- If necessary, use a spill containment tank in the event of an accidental leak
- Do not store chemically incompatible products mixed together
- Never stack products
Descaling plan
Whatever the process used, and in addition to staff training, a descaling plan should be drawn up in accordance with the following steps:- Study the water supply (where, quality, quantity)
- Make an inventory of the surfaces or installations to be treated (equipment, premises) and the materials in contact with them
- Determine the process and equipment required, as well as the methods of implementation (frequency of use, duration, time of day)
- Define the means of control (rinsing, results)
- Ensure operator safety (safety data sheet) and respect for the environment (control of effluent volumes and type)
It is essential to post safety and usage instructions in the areas concerned: equipment concerned, operation, frequency, product, dose, preparation, method of application, contact time, rinse test.
Experiment
See the list of experimentsSee more - Press release: Guide to Good Hygiene Practices - 2018
- Bioadhesion, cleanability and optimising the use of water in hygiene operations - 2017
- Hygiene and cleanability - 2016
- Optimising procedures through a better understanding of bio-adhesion phenomena - 2015
- Compendium of recommendations on good hygiene practice for consumers - 2013
- Preparing the cellar before the harvest - 2010
- Tidying up the cellars before the harvest - 2008
- Water logs: barrels - 2007
- Water notebooks: tanks - 2007
- Hygiene package and HACCP - 2006