Filter press
Filter presses are used to clarify products with a high particle content. They operate by self-filtration, with the impurities forming the filter medium. The process takes place in two phases: liquid-solid filtration and cake dewatering. The system uses a piston pump for the high-pressure feed, and trays lined with filter cloths form chambers for filtration. A scraper system facilitates filtrate removal and maintenance. Filtration aids can be added to improve performance and extend filtration cycles.
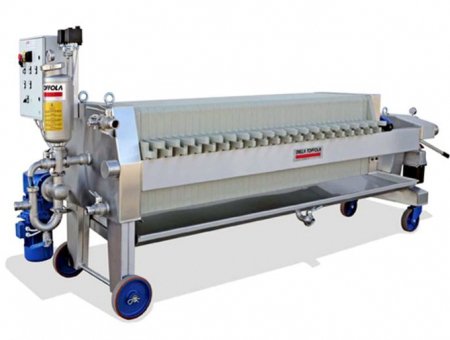
Filter presses
Designed for the clarification of charged products, filter presses feature a filtration cycle during which the pressure changes as the chambers fill.Clarification with a filter press is characterised by 2 essential phases:
- Filtration , which separates the liquid from the solid and ensures the clarity of the product
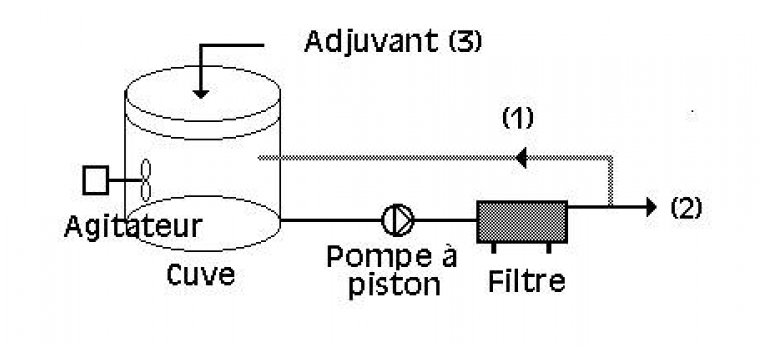
Typical use of a filter press
Filter presses work on the principle of self-filtration : it is the impurities retained on the support that constitute the filtering medium itself. This is the case when the filter is used without filter aid - diagram above: circuits (1) (loop circulation of the product to be filtered until the filtering layer is formed) and (2) (filtered product outlet).
The product to be filtered must have a sufficient load to ensure a stable cake and satisfactory clarification.The characteristics of the deposits to be retained determine the fineness of the filtration.
The addition of a filtering aid (perlite, kieselguhr, cellulose, etc.) ensures effective drainage, which delays clogging, guarantees higher volumes filtered/cycle and facilitates de-clogging - diagram above: circuits (3) and (2) (circuit (1) is then unused).
Technical presentation of a filter press
- pump
- filtrate collector
- plate equipped with its cloths
- steel frame
- filter cloth
- tank with pneumatic buffer
- central supply of liquid to be filtered
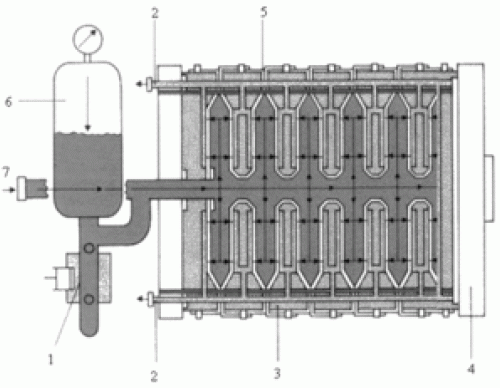
Diagram of a filter press
Main components
The trays
These are covered with a filter support cloth (nylon or polypropylene). The cloths must be rot-proof.Two trays placed side by side form a chamber in which the cake is formed. The cake can be 30 to 35 mm thick, depending on the volume of the chamber.
A hydraulic system (200-300 bar) is used to tighten the assembly, ensuring awatertight seal.
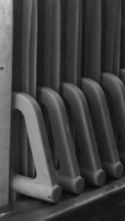
Discharge
The filtrate is evacuated through one or two ducts located at the corner of the plates and then collected on the sides of the filter.Note: for particularly clogging liquids, some manufacturers offer membrane trays to be inserted between the ordinary trays. The membranes are inflated with air or water, reducing filtration time and improving cake dewatering. However, membrane trays are rarely used in winemaking.
Conducting the filtration
- Prepare a volume of liquid to be filtered corresponding to one filtration cycle. It is not necessary, and not even advisable, to prepare a volume greater than the volume filtered per cycle.
- If necessary, incorporate the required quantity of additive directly into the liquid to be filtered.
- After adding the additive, wait 15 to 20 minutes before starting the filter to ensure that the perlite or diatomaceous earth is properly hydrated.
- Ensure that the liquid-adjuvant mixture iswell agitated throughout the filtration cycle (including preparation), to maintain total homogeneity. Any break in the cycle will lead to rapid clogging.
- The filter is unclogged when clogging occurs.
- Clogging, characterised by alternating stops and starts of the piston pump, can be considered complete when the time between a stop and a restart reaches approximately 45 seconds.
carrying out a cycle
A normally optimised working cycle should not exceed 3 to 4 hours:- 15 to 20 minutes for start-up
- 90 to 180 minutes filtration
- 20 to 40 minutes cleaning
Table: Average filtration cycle characteristics
It should be noted that the flow rates per cycle generally observed depend on :
- the load of products to be filtered
- pressing methods (variations of 20 to 45% in flow rates per cycle).
- the characteristics of the filter used:
- filtering surface
- type of cloth
- the feeding system
- oenological treatments (enzyming, etc.).
Special case of alluvial filtration with a filter press
The filter press can be used to clarify new wines, press wines, fermenting wines or wines in the process of being made: it then behaves like a continuous alluvial filter.There are three possible operating schemes:
1 - Addition of an alluvial tank with agitation, a dosing pump and a continuous flow pump for the wine feed. The piston pump is then not used: this is the most suitable solution
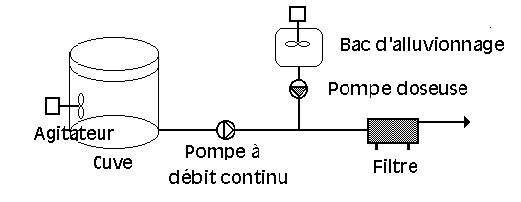
2 - The piston pump is usedfor alluviation.
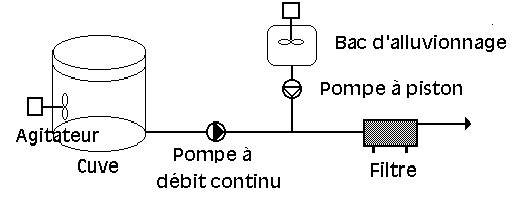
3 - The additive is added to all the wine to be filtered. It is pumped in a closed circuit (1) until the filtrate has cleared, before being sent to the reception tank (2).
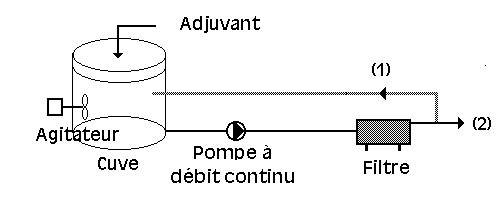
Choosing the right equipment
Defining the filter best suited to your needs means first and foremost answering the following questions:- What is the daily volume to be treated?
- How many cycles can be used?
- What types of product do you want to clarify?
Resolving malfunctions
Filtration quality is inadequate (cloudy filtered product)
- Check the integrity of the cloths
- Check that the trays and cloths are correctly positioned
- Adjust the filter medium if necessary.
Abnormal leakage of wine
- Check that the cloth(s) are correctly positioned
- Tighten the filter if necessary
- If necessary, improve the peripheral seal of the cloths.
The cakes are not drying properly
- The quantity of additive is too low
- Increase the quantity of filter aid
- The cloths are not properly descaled
- Clean the cloths
- The number of trays is too high in relation to the volume used
- Reduce the number of trays.
Pressure increases too quickly (cycle too short)
- Quantity of additive too low
- Increase the quantity of additive
- Cloths are scaled
- Clean properly
- Insufficient number of trays
- Increase the number of trays if possible
- Check that the product + additive mix is correct
- Filtering additive unsuitable
- Change the additive