Chilled water system
A wine-making chilled water system is a cooling system used to control temperatures during winemaking. It produces chilled water (between 0 and 6°C) which is distributed via a network of pipes to regulate the temperature of the fermentation tanks. This control is essential to prevent the heat released by fermentation from exceeding critical thresholds, which could alter the aromas, flavours and quality of the wine. The system provides precise and constant cooling, which is essential for the production of quality wines, particularly during periods of high ambient temperatures.
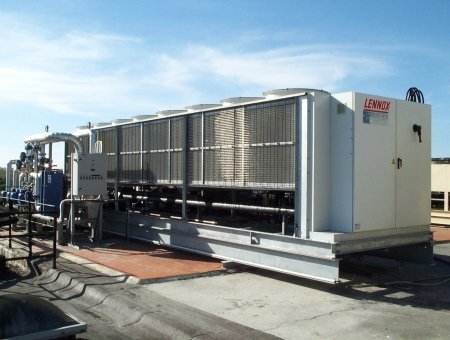
Main components
The compressor
Traditionally, compressors used in the wine industry are hermetic or semi-hermetic piston compressors, which transform rotary motion into reciprocating motion, or hermetic or semi-hermetic rotary compressors. These compressors cover a wide power range.For small and medium power ratings (< 200 kW), there are also scroll-type rotary compressors, which have the advantage of having fewer moving parts than a piston compressor and are also quieter.
Finally, for high power ratings (200 to 1400 kW), screw compressors offer a better coefficient of performance (C.O.P = Ratio of cooling capacity to electrical power input (Qf/Qe)) than reciprocating compressors.
Note : the difference between a semi-hermetic and hermetic compressor lies in the fact that certain components of the semi-hermetic compressor are accessible on site, whereas the hermetic compressor must be returned to the factory for repair.
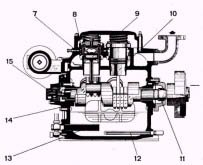
Diagram of a piston compressor
Semi-hermetic piston compressor
7 - Power reduction device
8 - Annular suction valve
9 - Piston pin
10 - Piston
11 - Seal
12 - Oil heater
13 - Oil pump suction strainer
14 - Crankshaft
15 - Oil pump
7 - Power reduction device
8 - Annular suction valve
9 - Piston pin
10 - Piston
11 - Seal
12 - Oil heater
13 - Oil pump suction strainer
14 - Crankshaft
15 - Oil pump
The condenser
The air-cooled condenser
The air-cooled condenser is generally made up of a serpentine tube fixed vertically to a metal sheet and one or more fans placed at the top of the cooling unit. The air flow rate through a condenser depends on the amount of heat to be removed. The number of fans serving a condenser depends on its shape (for the same surface area, a long condenser requires more fans than a short one).The fans used on outdoor units are of the helical type.
The fans used on units located inside buildings are of the centrifugal type and can supply hot air exhaust ducts.
Water-cooled condenser
The refrigerant and water circulate in counter-current in tubes placed one inside the other. Other types exist (such as the multi-tube condenser), but the principle is identical.
The overall heat exchange coefficient K of water is higher than that of air: for the same heat capacity, water-cooled condensers take up less space than air-cooled condensers.
Their use in the wine industry is severely restricted by the latest water laws.
The overall heat exchange coefficient K of water is higher than that of air: for the same heat capacity, water-cooled condensers take up less space than air-cooled condensers.
Their use in the wine industry is severely restricted by the latest water laws.
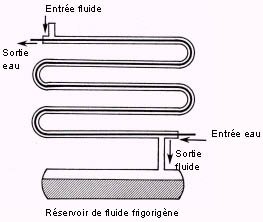
Diagram of a double-tube condenser
The evaporator
This is an exchanger that transfers heat from the water to be cooled to the refrigerant. Some are placed in the buffer tank containing the water to be cooled (coil type exchanger).Others form a secondary circuit (plate, coaxial or multi-tube exchangers).
The characteristics of these exchangers are described in the "External exchangers" and "Internal exchangers, belts, double jacket" sections.