On-board destemmer and sorter
The on-board destemmer and sorter is an essential tool on grape harvesting machines, designed to separate berries from vegetation debris and green waste. Using technologies such as vibratory de-stemming and roller sorting tables, it allows free berries and juice to fall into the skips, while stalks, petioles and other waste are ejected. The main aim of this equipment is to improve the quality of the harvest by eliminating undesirable elements right from the plot, thus avoiding undesirable tastes in the must.
The performance of the on-board de-stemmer is crucial to ensuring a clean, high-quality harvest. Precise settings, such as vibration frequency and gin rotation speed, play an important role in sorting efficiency and minimising berry losses. Regular and careful maintenance of the gin is also essential to maintain its efficiency and ensure an optimum harvest.
The performance of the on-board de-stemmer is crucial to ensuring a clean, high-quality harvest. Precise settings, such as vibration frequency and gin rotation speed, play an important role in sorting efficiency and minimising berry losses. Regular and careful maintenance of the gin is also essential to maintain its efficiency and ensure an optimum harvest.
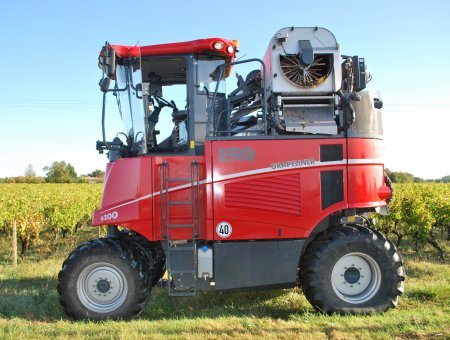
The equipment
From the first very simple sorters to the latest systems combining destemming, sorting of coarse elements and elimination of small-sized waste, the performance of on-board sorters has become a key factor in controlling the quality of mechanical harvests . As the harvesting machine produces a crop that includes intact berries, shattered berries, juice, whole leaves, pieces of leaf, petioles and bits of vine shoot, the need to obtain a quality crop that is less polluted became a major challenge.
The first step was to install simple devices on the harvesting machines to extract anything that was large enough or had a large enough surface area to be sucked up. To improve the efficiency of this sorting by suction, the Pellenc company developed the sorter, consisting of a rotating mesh belt through which the harvest from the conveyors drained, with the free berries and juice falling into the skips, while the rest (bunches and fractions of bunches, leaves, etc.) were subjected to the suction of fans.
A similar system was later adopted by the manufacturer Alma under the name central sorting and cleaning unit. However, items too small to be retained by the belt grid still had to be eliminated.
While Grégoire had previously offered optional de-stalkers on its machines, the arrival on the market of the SOCMA on-board de-stalker on New-Holland Braud grape harvesters marks a new stage in the development of de-stalkers. This on-board de-stemmer incorporates the principle of the rotating grid, which allows free berries and juice to fall into the skips before the rest of the harvest is processed in a de-stemmer made up of flexible fingers mounted on horizontal axes. The stalks and other undesirable elements are ejected behind the machine. The results obtained with this machine are also impressive, with destemming efficiency comparable to that of winery equipment, and more leaves and shoots removed.
The competition couldn't stand still, either, with Pellenc and Gregoire both offering, on their respective machines, systems that integrate de-stemming after a draining or pre-sorting phase.
A further step was taken in 2007 with the arrival on the market of the Pellenc Selectiv'Process, which completely changes the approach to de-stemming and on-board sorting on grape harvesting machines. On the one hand, the method of destemming has been completely changed, as it is now carried out by vibration, and on the other hand, sorting has been redesigned to eliminate the most difficult elements to manage, the stalks. A sorting table covering the bins, made up of crenellated rollers between which the berries can fall, has the role of aligning the petioles and guiding them towards the side edge of the bins where they are ejected.
This race for performance has led to new developments at Grégoire and New-Holland, with some differentiation in the technology used to further improve the cleanliness of the harvest, but also some similarities, such as the use of rollers to align waste that is not very sensitive to suction. Grégoire's Cleantech Vario and New-Holland's Optigrape use the same principle, but supplement it with a soft-finger de-stemmer in one case, and a plate blower system in the other (the part that doesn't go into the on-board de-stemmer).
Another player on the market, ERO, has also been offering a machine equipped with a destemmer for a number of years. This machine has recently been fitted with a roller sorting table , which does additional work.
The first step was to install simple devices on the harvesting machines to extract anything that was large enough or had a large enough surface area to be sucked up. To improve the efficiency of this sorting by suction, the Pellenc company developed the sorter, consisting of a rotating mesh belt through which the harvest from the conveyors drained, with the free berries and juice falling into the skips, while the rest (bunches and fractions of bunches, leaves, etc.) were subjected to the suction of fans.
A similar system was later adopted by the manufacturer Alma under the name central sorting and cleaning unit. However, items too small to be retained by the belt grid still had to be eliminated.
While Grégoire had previously offered optional de-stalkers on its machines, the arrival on the market of the SOCMA on-board de-stalker on New-Holland Braud grape harvesters marks a new stage in the development of de-stalkers. This on-board de-stemmer incorporates the principle of the rotating grid, which allows free berries and juice to fall into the skips before the rest of the harvest is processed in a de-stemmer made up of flexible fingers mounted on horizontal axes. The stalks and other undesirable elements are ejected behind the machine. The results obtained with this machine are also impressive, with destemming efficiency comparable to that of winery equipment, and more leaves and shoots removed.
The competition couldn't stand still, either, with Pellenc and Gregoire both offering, on their respective machines, systems that integrate de-stemming after a draining or pre-sorting phase.
A further step was taken in 2007 with the arrival on the market of the Pellenc Selectiv'Process, which completely changes the approach to de-stemming and on-board sorting on grape harvesting machines. On the one hand, the method of destemming has been completely changed, as it is now carried out by vibration, and on the other hand, sorting has been redesigned to eliminate the most difficult elements to manage, the stalks. A sorting table covering the bins, made up of crenellated rollers between which the berries can fall, has the role of aligning the petioles and guiding them towards the side edge of the bins where they are ejected.
This race for performance has led to new developments at Grégoire and New-Holland, with some differentiation in the technology used to further improve the cleanliness of the harvest, but also some similarities, such as the use of rollers to align waste that is not very sensitive to suction. Grégoire's Cleantech Vario and New-Holland's Optigrape use the same principle, but supplement it with a soft-finger de-stemmer in one case, and a plate blower system in the other (the part that doesn't go into the on-board de-stemmer).
Another player on the market, ERO, has also been offering a machine equipped with a destemmer for a number of years. This machine has recently been fitted with a roller sorting table , which does additional work.
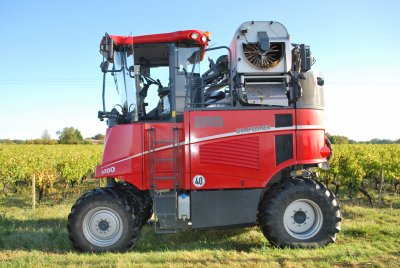
On-board sorter - Ero
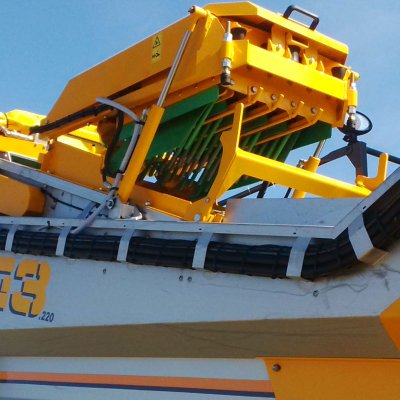
Vibrating fingers on destemmer - Gregoire
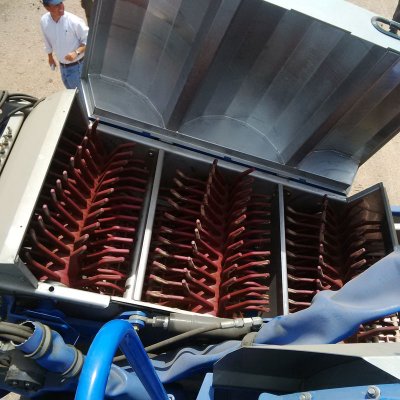
Rotors on the on-board grader - Scoma
Technical advantages
The quest for very high sorting performance goes hand in hand with a very thorough quality approach right from the plot, and can be supplemented by sorting in the cellar to achieve a zero defect level in the vat. Eliminating green matter very early on is one way ofavoiding the transfer of undesirable flavours into the must. This is all the more true when the distance between the plot and the winery is great (prolonged contact during transport) and when the liquid phase in mechanical harvesting encourages contact between the grapes and the rest.However, the risk of aromatic deviations in the wines remains moderate with the levels of waste commonly observed in the skips of today's harvesting machines. The stakes and benefits of on-board sorting equipment therefore vary according to the profile of the user: a private individual using a service provider for harvesting may require an on-board sorter on the machine to guarantee a certain level of cleanliness. A cooperative will only be interested in making this investment if the payment made to the winery is differentiated according to the quality of the grapes and the cleanliness of the harvest. Some customers will question the presence of a destemmer in the cellar, and the most demanding will use machines equipped with sorters as a prerequisite to table sorting, whether automated or not, to guarantee highly selective vatting.
Disadvantages
The downside of installing sorters to extract waste is the risk of losing berries during destemming and waste ejection. This parameter was measured during our trials. It averaged 0.26% of the total harvested mass, varying from year to year from 0.11% to 0.4%. This represents between 8 and 32 kg for a yield of 8 tonnes per hectare, for example.Maintenance
The hygiene of the grape harvesting machine is an important point, and the presence of the sorters requires thorough cleaning, as they represent additional areas of material accumulation (skins, sugar, green waste) compared with more basic machines.Settings
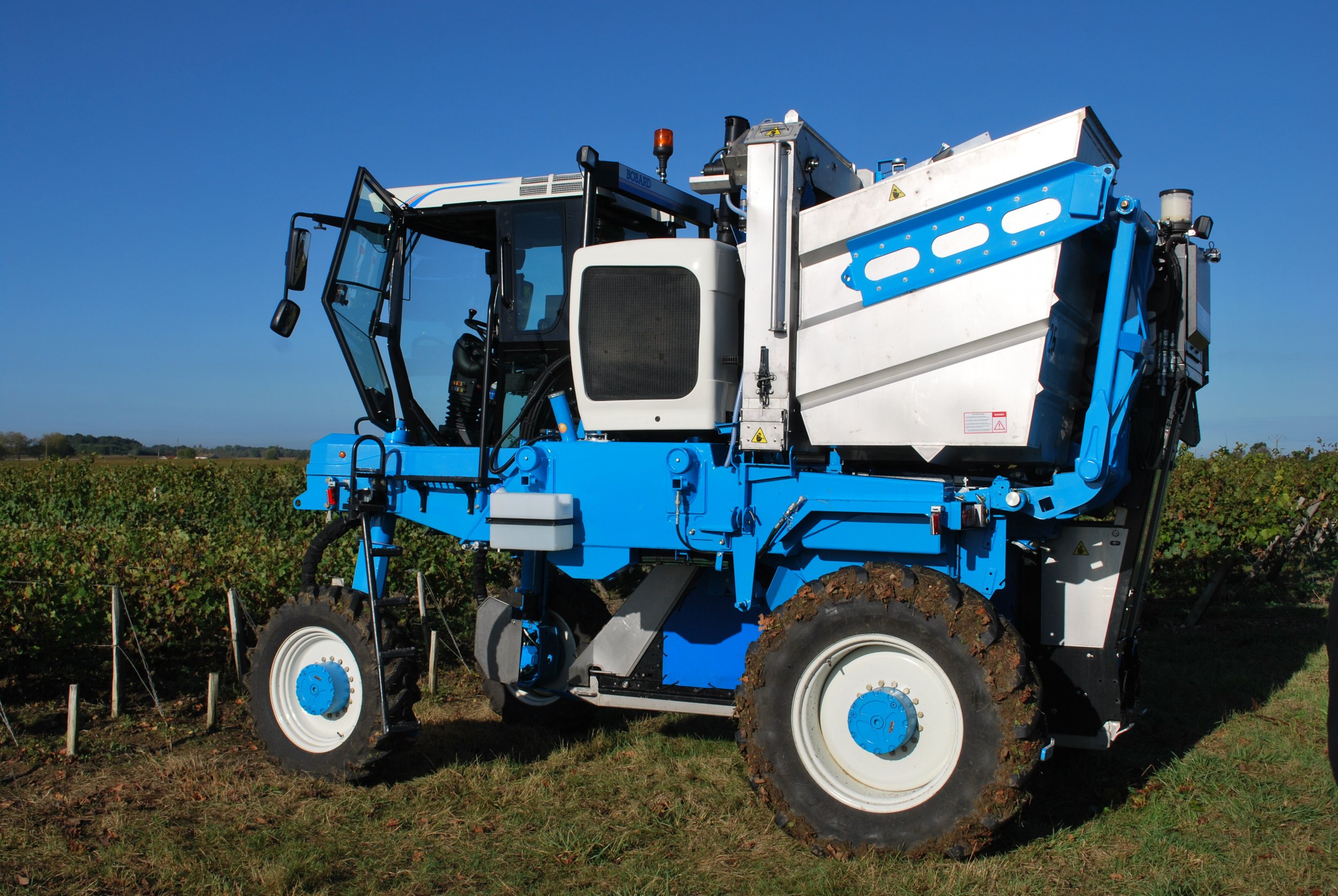
Onbard sorter - Bobard
Sorters have their own settings : frequency of vibration or speed of rotation of the gins, roller spacing, air speeds are all parameters that will affect cleaning efficiency as well as the rate of loss.
To a certain extent, they make it possible to correct imperfect machine shaking settings, as they eliminate a lot of waste.
However, it should not be forgotten that the most important way of improving harvest quality is still to set the harvesting head parameters correctly, depending on the vine and the degree of ripeness of the grapes.
To a certain extent, they make it possible to correct imperfect machine shaking settings, as they eliminate a lot of waste.
However, it should not be forgotten that the most important way of improving harvest quality is still to set the harvesting head parameters correctly, depending on the vine and the degree of ripeness of the grapes.
Experiment
See the list of experimentsSee more