Grape harvesting machine
Grape harvesting machines, consisting of a motorised chassis and a harvesting head, mechanise the harvesting of grapes by shaking the vines to detach the berries.
These machines use shaking, receiving and conveying systems to transfer and clean the grapes, minimising the need for labour. The versatility of the carriers, allowing the machine to be used for other tasks outside the harvesting period, helps to amortise the high cost of the equipment.
Careful management and precise adjustments are essential to ensure a quality harvest.
These machines use shaking, receiving and conveying systems to transfer and clean the grapes, minimising the need for labour. The versatility of the carriers, allowing the machine to be used for other tasks outside the harvesting period, helps to amortise the high cost of the equipment.
Careful management and precise adjustments are essential to ensure a quality harvest.
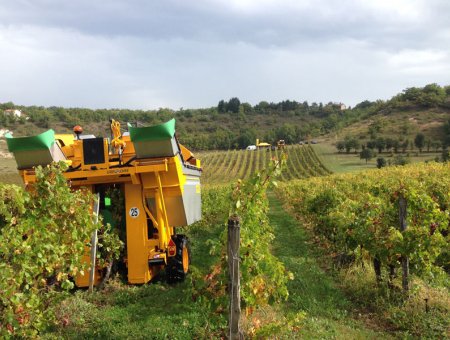
Technical presentation of a grape harvesting machine
A grape harvester consists of a chassis for traction and transport and a harvesting head. The chassis is either self-propelled or towed. The harvesting head is the most important component. It consists of the shaker, the grape reception, a system for transferring the grapes to the skips, the skips themselves and the cleaning devices.Shaking
Harvesting machines harvest by transmitting sufficient energy to the vines to detach the berries from their pedicels.
Lateral shaking has emerged as the most effective system. Two rows of shakers keep the vegetation in line with the trellising. The shaking is transmitted by a crank-crank system or by jacks acting on the shaft to which the shakers are attached. The shaking parameters are frequency, amplitude and toe-in.
Each manufacturer has developed its own shaker shape and mode of operation, with a few constants: the flared shape created by aligning the shakers at the front of the harvesting head enables the vegetation to be progressively compressed, held in place and the energy transmitted for the berries to be removed. The shape or fixing of the shakers at both ends prevents excessive movement, which would be a source of breakage in the vegetation (whiplash effect).
Lateral shaking has emerged as the most effective system. Two rows of shakers keep the vegetation in line with the trellising. The shaking is transmitted by a crank-crank system or by jacks acting on the shaft to which the shakers are attached. The shaking parameters are frequency, amplitude and toe-in.
Each manufacturer has developed its own shaker shape and mode of operation, with a few constants: the flared shape created by aligning the shakers at the front of the harvesting head enables the vegetation to be progressively compressed, held in place and the energy transmitted for the berries to be removed. The shape or fixing of the shakers at both ends prevents excessive movement, which would be a source of breakage in the vegetation (whiplash effect).
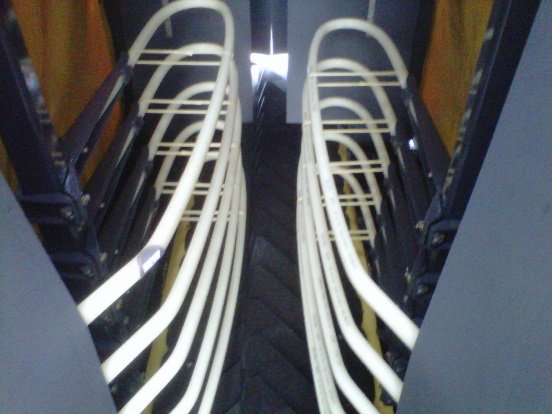
Shakers
Receiving the grapes
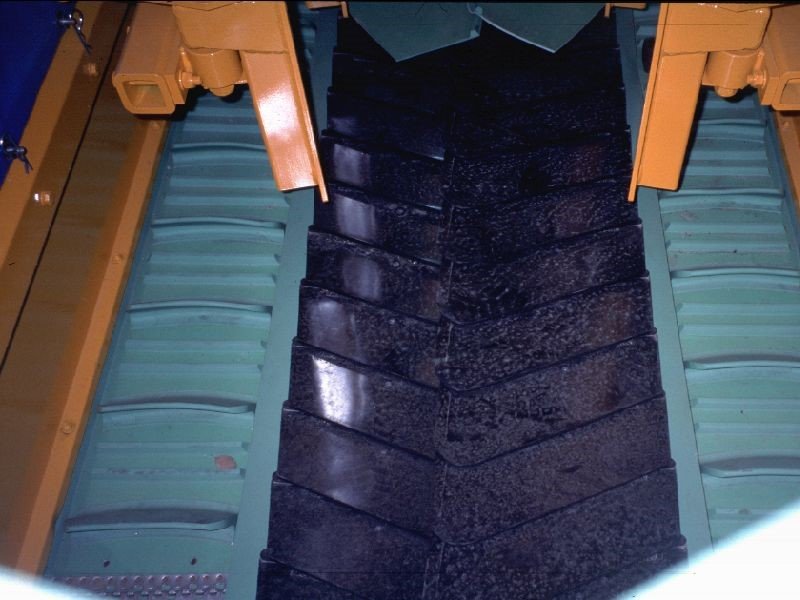
Reception and transfer of the harvest onto conveyor belts
Depending on the manufacturer, the grapes are received and the harvest head sealed by a ramp of partially overlapping articulated scales or by a series of flexible buckets surrounding each vine. The scales are inclined towards the transfer system(conveyor belts).
The noria of flexible buckets plays the role of reception and transfer, rotating in the harvesting head in inverse proportion to the machine's forward movement. In this way, the buckets have zero movement in relation to the stock.
Simple conveyor belt
Conveying by conveyor belt involves a specific design of the cleats on the rotating belt to retain both the grapes and the juice. The grapes are spread out on the belts so that they can be cleaned by lower hoovers before the leaves to be extracted become too soaked with juice.Conveyance by noria of buckets
Before the grapes are emptied into the bins, they are spread out on a rotating conveyor belt, which sends the flow of grapes under a hoover, allowing the leaves to be extracted as the material falls.Cleaning systems
There are several types of cleaning device:vine shoot traps, hoovers, sorters and gins.They can all be present on the same harvesting head. The principle is simple: spread out the raw material to make it easier to suck up the leaves, drain on a grid to separate the liquid phases and free berries from the bunches and fractions of bunches, align the undesirable elements to encourage their elimination before falling into the skips.
On-board gins use either vibration or the rotor-cage principle. In addition to removing the stalks, they also remove more debris. The other components of the grape harvesting machine are those that provide more or less easy access for adjustments and daily cleaning of the various components: hatches, openings, ladders and platforms.
what are the manufacturers' strategies in this area?
Definition:
A grape harvester is said to be multi-purpose when, without its harvesting head, it is fitted with one or more pieces of equipment that allow the chassis to be used outside the harvesting period. The most common applications are spraying and pre-pruning.
Multifunctional equipment consists of equipping the chassis with at least two separate pieces of equipment that can work together.
Examples:
- Benefits: saves time, cushions the machine over prolonged use, better positioning of tools by straddling the row, etc
- Make the chassis more profitable
- Work more rows in one pass, faster, for more surface area
- Carry more loads (autonomy) or more equipment
- Better positioning of equipment on the row
- Specific equipment assembly
- Equipment is sometimes less expensive (because it requires less adaptation than a row spacing mast) and sometimes more expensive because it is more specific
- Counterweight on the machine (same as inter-row)
- Heavy chassis: settling
- Pellenc: Pellenc self-propelled machines are versatile by design, so all types of equipment are covered
- At New-Holland, versatility has been developed around pre-pruning and spraying, in co-design with Provitis and Berthoud
- Grégoire has developed the versatility of its grape harvester chassis with the acquisition of Lagarde and Paris. However, its range still includes machines dedicated solely to harvesting
- Alma has joined forces with an Italian specialist in high-clearance chassis to concentrate on its range of towed machines
Impact on costs of multi-purpose use:
- Increase in the number of hours the chassis is used: reduction in the hourly cost of towing with the chassis. The cost is spread over several operations and not concentrated on the harvest
- If the passage speed is higher, work times are shorter
- Significant savings if combined operations (multifunction)
- Higher fuel consumption due to more powerful engine
What are the most important parameters for guaranteeing harvest quality?
The action of the grape harvester consists in transmitting, by shaking the vegetation, the energy needed to detach the berries from the stalk. Ideally, mechanical harvesting is the result of removing the bunches of grapes from the stalk. In practice, however, the fragility of the stalk of the bunch at the time of harvest and the mechanical impact of the harvesting head on all the vegetation and the trellising means that the result is made up of bunches and fractions of bunches, destemmed berries (whole or split), juice and a number of undesirable elements such as leaves, petioles, bits of vine shoots or other elements from the trellising.The harvest is more or less liquid and the exchanges between the must, the skins, the oxygen in the air and the various elements that can be found are affected. So when harvesting whites, it is particularly important to do everything possible to limit oxidation : protection with dry ice or dilution of SO2.
To avoid the possible negative impacts of mechanical harvesting, the first thing to do is to take action on the vine and the trellising. The vineyard must be adapted to mechanisation, not the other way round. Particular attention needs to be paid to the stakes, which will be subjected to considerable stress, and which must be able to transmit the shaking energy. The upright position of the vegetation is more favourable to the passage of the machine than a drooping position, with which the shoots are more exposed to breakage. Finally, it should be borne in mind that the ties and staples for the lifters will also be subject to breakage to a greater or lesser extent.
The state of health in the vineyard is particularly important , as the machine does not sort out what it drops, and the activity of grey rot, for example, is particularly harmful.
Finally, it is at the level of the machine and its use that the parameters necessary for good harvest quality are refined, taking into account the characteristics of the vine and the grapes.
Here are some useful definitions for setting up a grape harvester
- Pinch : incompressible thickness of vegetation on the row. This is the minimum distance between two shakers on either side of the harvesting head. It must be wide enough to hold the vines well during shaking, not too tight to avoid pulling on the shoots, and not too loose, otherwise the vines are beaten but not shaken.
- Shaking frequency: number of shaking cycles per minute. Together with the forward speed, this parameter defines the number of shaking pulses per metre travelled.
- Amplitude: this parameter defines the length of the stroke of a shaker in motion. Amplitude has a very strong impact on the energy transmitted for unhooking.
Adjusting the machine in just a few steps
- Adapt the number and position of shakers to the fruit-bearing zone: there is no point in exploring a wider zone, as this will increase the quantity of leaves removed.
- Set your forward speed moderately: around 3 km/h. Speed is the enemy of harvest quality, as it accentuates mechanical impacts.
- The shaking frequency should be adjusted in steps of 10 strokes per minute, depending on how difficult it is to remove the berries and also on the forward speed, so as to maintain a sufficient number of shaking cycles per metre.
- Amplitude: apart from extreme cases, it's best not to play with this parameter too much, as it has a very strong impact.
- Speed of the grape harvest conveyors to spread out and clean the harvest efficiently.
- Power of the hoovers used to remove leaves and other debris: a compromise needs to be found between high power and the suction of juice by monitoring the flow through the exhaust nozzles.
- Driving: a harvesting head is a heavy piece of equipment with a certain amount of inertia. A certain amount of clearance is allowed, but alignment with the row remains the best way of minimising the impact on the vegetation.
How does mechanical harvesting compare with manual harvesting in certain cases?
Numerous trials carried out in different wine-growing regions have shown that, in most cases, mechanical harvesting produces wines that are perfectly comparable to those produced by hand. The human factor remains paramount in guaranteeing this quality, as poor adjustments can also degrade the result. There are, however, special cases where this is more difficult, although possible: carbonic maceration, for example, which requires sufficient whole bunches.Safety
Working around a grape harvesting machine presents certain risks. People working near the machine are exposed to the risk of being crushed (due to lack of visibility) or thrown (due to extractor fans blowing).A safety perimeter must be set up at the start of the harvesting operation to limit these risks (10 m around the machine). Before carrying out any operation on the harvesting head, anyone working on the machine must ensure that the engine and moving parts such as extractors have come to a complete stop. Finally, no-one should be on the machine when it is harvesting. The high access points on the harvesting head are reserved for cleaning or dismantling operations.
Storage
The harvest has just finished, so if you want to keep your grape harvester at its full potential and avoid any problems when you start up again, a few precautions need to be taken.
There's no need to remind you that a thorough cleaning is essential, and that this should be carried out using a high flow of water at low pressure. A high-pressure cleaner should be avoided, as the pressurised water will penetrate the bearings and electrical connections.
The machine should be greased immediately after cleaning, as the bearings are not rustproof and the cleaning water oxidises very quickly. Don't forget to grease the legs thoroughly with a quality grease (graphite grease, for example) to prevent them seizing up.
There's no need to remind you that a thorough cleaning is essential, and that this should be carried out using a high flow of water at low pressure. A high-pressure cleaner should be avoided, as the pressurised water will penetrate the bearings and electrical connections.
The machine should be greased immediately after cleaning, as the bearings are not rustproof and the cleaning water oxidises very quickly. Don't forget to grease the legs thoroughly with a quality grease (graphite grease, for example) to prevent them seizing up.
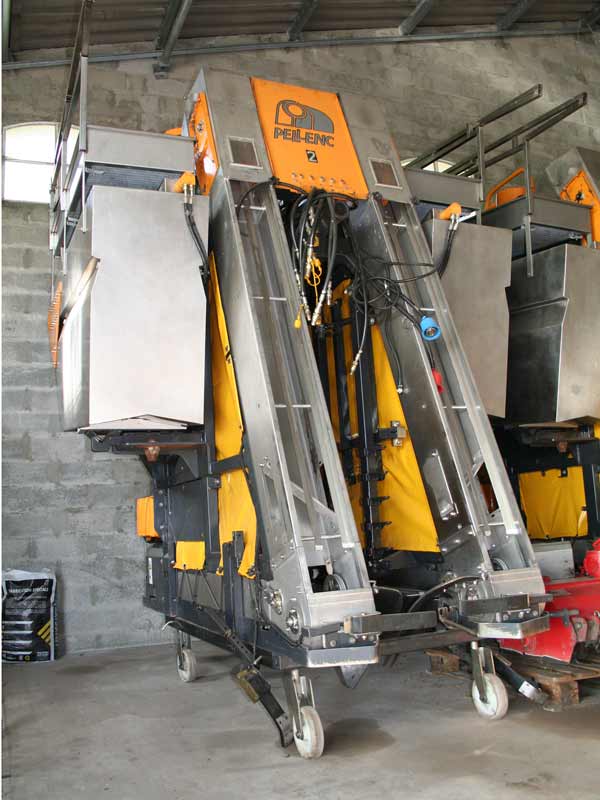
Harvesting head in storage
Conveyor belts
Conveyor belts should be dismantled and stored flat or in wide-core rollers in a dry room away from light.Norias
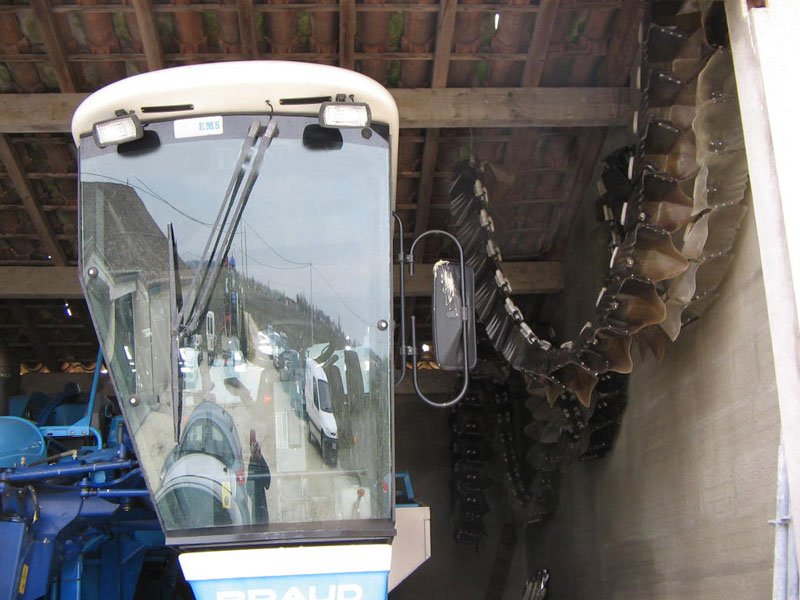
Norias dismantled from the harvesting machine
Norias should be stored dismantled from the machine, attached by their links to the beams of a shed, for example (storing them in a heap causes deformation and a loss of watertightness as they rise to the rear of the machine).
When dismantling the norias, oil the rails to prevent them from rusting (rust causes rapid wear to the runners when they are restarted).
On ALMA machines, it is advisable to grease the conveyor chain with edible grease.
Shakers
Every year we still come across a considerable number of shakers that have to be reformed, this is particularly true for the old GREGOIRE shakers but also for the PELLENC shakers, the material making up the shakers tends to want to return to its initial shape (right). If they are left assembled without being clamped with rilsan collars (be careful, they can come loose), wide packaging adhesive, or even wire, they slowly return to their original shape and reforming becomes necessary. PELLENC recommends installing a chevron to clamp the shakers every evening after work.On New-Holland - BRAUD machines, check the wear rating of the straw walkers to prevent them from breaking, which can cause damage (see instructions).
The diesel fuel tank must be filled up before wintering the machine to avoid condensation in the tank.
The battery charge should be checked every month or so.
It is advisable to run the machine every month, activating all the hydraulic systems to remove any drops of water caused by condensation in the tanks, or sometimes by the introduction of water when cleaning the machine. On this subject, it should be pointed out that if the hydraulic oil appears cloudy, it is often polluted by water, and it is advisable to change it.
Overhaul
Don't wait until the last minute!All too often, we worry about getting the machine back into working order before we go on holiday - it's too late. It's also the holiday period for dealers, and workshops are overloaded. Don't wait until the last minute, be smart and take advantage of the off-season prices for machine servicing. If your carpets are damaged, have them repaired.
Intensive use of grape harvesting machines generates maintenance costs that you don't have to deal with for specific use in grape harvesting, so you might think of reconditioning an engine in intensive use at around 6,000 hours or, on certain machines, rebuilding the leg bushes for 3,000 hours of use. On machines with the least robust chassis, some users have noted structural fatigue caused by intensive use at working speeds higher than those used during harvesting.
Hygiene
Daily cleaning of the machine is essential.Sugars and other plant residues are breeding grounds for micro-organisms that can spoil the quality of the harvest. Without going as far as disinfecting, you need to eliminate the worst of it. To do this, start by removing visible clumps manually or with a brush, to save time and water. The flow rate must be high and the pressure low to avoid damaging the bearings. Between 2 and 3 m3 of water are needed to clean a grape harvester completely. The systems integrated into the harvesting heads do provide an interesting rinse, but their action alone is insufficient.
You need to be aware that this is a significant source of pollution, even if it's only organic matter (sugars, plants). This pollution is all the more significant if it is concentrated in a very specific area, as is the case with collective cleaning areas. These areas have the advantage of being well designed for optimal cleaning, and the pooling of the installation is attractive from a financial point of view. The need to take the environment into account means that we need to think more carefully about our practices in this area. For example, we can envisage mixed solutions combining an initial cleaning of the machine on the plot and a final cleaning at a washing area. In this way, part of the effluent is spread on the plot and the concentration on the collective area is reduced. This requires a mobile clear water tank to accompany the harvesting site.
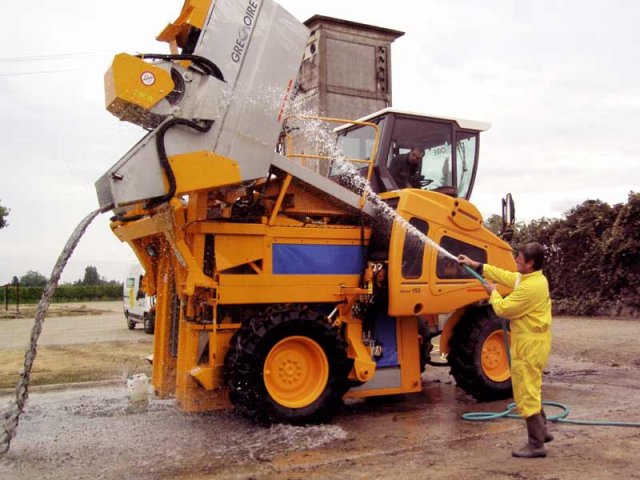
Cleaning a grape harvesting machine with a water jet
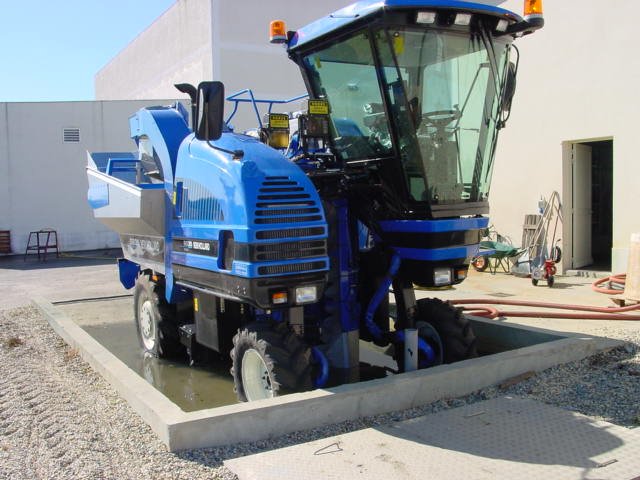
Experiment
See the list of experimentsSee more