Precision pruning
With a view to reducing production costs, the mechanisation of vine pruning is tending to develop, especially in local wine appellation areas. Mechanical pruning machines, which are much more sophisticated than traditional pre-pruners, enable the vines to be pruned with two clear eyes, precisely following the cordon. Various technologies are available on the market, with cutting bars or circular saws, and some incorporate advanced systems such as Visio bead tracking. These innovations make pruning machines much easier to use and more efficient, while reducing the need for manual intervention.
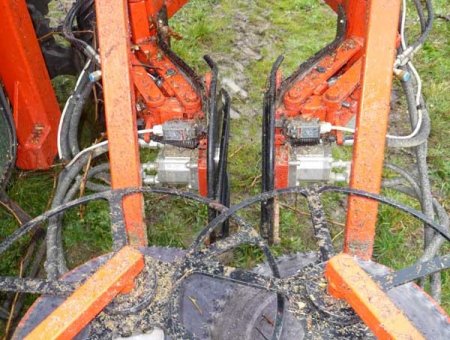
Work objective
With a view to reducing production costs, mechanised pruning is tending to develop. For the moment, however, it is only possible in local wine appellation areas. More than just improved pre-pruners, mechanical pruning machines are capable of pruning with two free eyes, following the cordon as closely as possible.Various machines are available, with cutting bars (Chabas) or circular saws (Pellenc, CGC AGRI, Brunel, Ferrand, etc.). Pellenc sets itself apart from other manufacturers by offering a Visio bead tracking system. Automated cord tracking and stake detection greatly facilitate the use of mechanical pruning machines.
The cutting modules are fed hydraulically. The flow required to drive the circular saws justifies the use of a hydraulic power pack.
Components of the pruning machine
Cutting modules
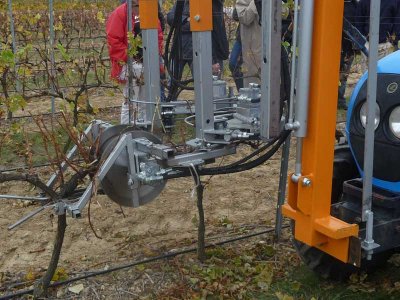
The aim of the cutting modules is to prune very close to the cordon, with 1 or 2 free buds, in order to keep manual labour to a strict minimum, i.e. 8 to 12 hours per hectare compared with 35 to 50 hours for conventional vine management.
The vertical and horizontal cutting modules are either circular saws or reciprocating cutting bars.
The relative position of each cutting module is a differentiating factor between machines. Integration into the pre-cutting process is possible.
The vertical and horizontal cutting modules are either circular saws or reciprocating cutting bars.
The relative position of each cutting module is a differentiating factor between machines. Integration into the pre-cutting process is possible.
Circular saws
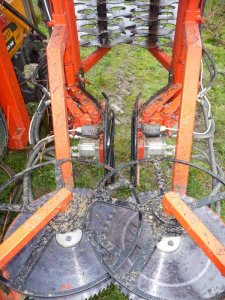
- Clean cut of shoots that cannot be resawed manually
- Cuts stalks (branches of old wood) on old vines
- Requires high rotation speed
The cutting bar
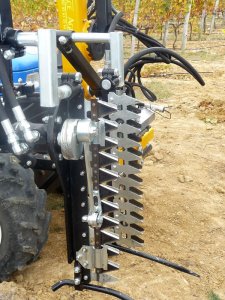
- Clean cut
- Low projection
- Low noise
The motors
These cutting modules are powered by hydraulic or electric motors (PELLENC machines until the end of 2012), which produce clean cuts at high rotation speeds.The positioning of the motors in relation to the circular saws (above or below) is part of the overall ergonomics of the machine.
Stake opening
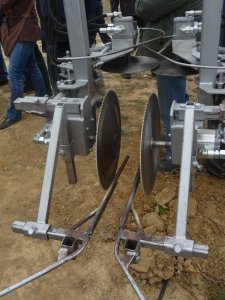
For pruners that can be used on free-standing or trellised vines, it is essential to have a device that opens at the stakes, both for the cutting module and the pre-pruning module.
These are either mechanical systems using support and bypass, which is easy given the low forward speeds, or hydraulically-assisted systems using sensors.
Illustration of the guide rails in the foreground and the guides that allow the horizontal saws to move out of the way when passing a stake in the background.
Bead tracking
The systems used to track the cord as closely as possible are designed to :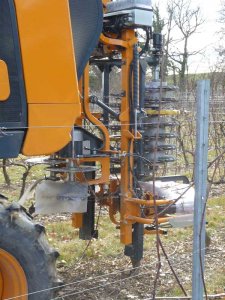
Height tracking :
- Pellenc only with Visio
- Otherwise manual
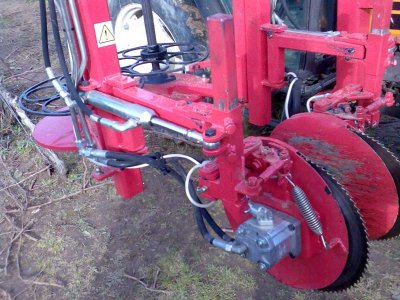
Lateral support
- Guide rails (all except CGC Agri)
- Gas springs (Pellenc)
- Springs (Cellier Boisset, CGC Agri)
- Double-acting probes and cylinders (CGC Agri)
Guide rails
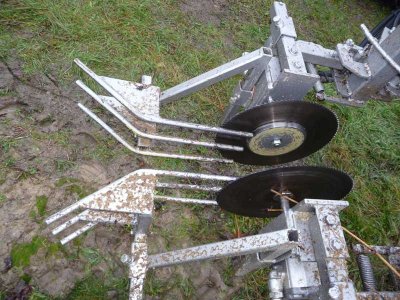
These long pieces keep the machine in line with the row of vines, by resting on either side of the vines on at least two consecutive vines.
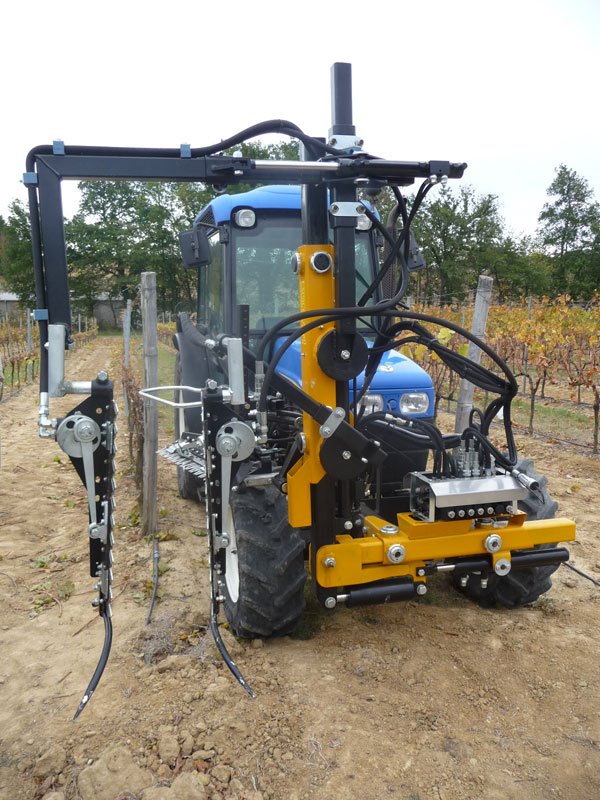
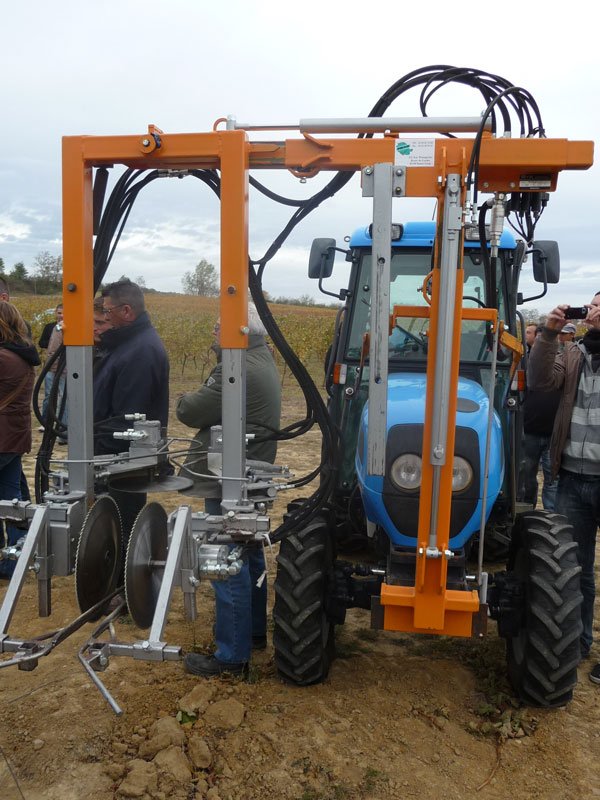
Adjustment and use of the pruning machine
Mechanised pruning requires a great deal of concentration on the part of the operator, as the machine passes as close as possible to the cordon in order to make a two-eye pruning. Most manufacturers offer manual cordon following, so it's a good idea to keep the cordons as straight as possible. In addition, mounting the machine between the wheels will give the operator better visibility.Thehydraulic equipment on the tool-holder mast allows the pruning module to be moved up and sideways. The post can be opened mechanically with assisted release (wheels, rollers, daisies) or automatically (Pelenc Visio system). Various systems are available for lateral tracking of the bead: guide rails (all except CGC AGRI) or probes and double-acting cylinders (CGC AGRI).
Mechanical pruning machines should not be used on plots where the trellising is of mediocre quality, as the machine is guided laterally by the row. Forward speed is low (around 2 km/h) and hydraulic requirements are fairly high, with oil flow rates generally in excess of 40 l/min.
The different ways of mounting short-cutting machines
- Mounted on a straddle carrier
- Mounted on inter-row, rear 3-point linkage
- Mounted on an inter-row, front multifunction mast
Mechanised pruning
Even partial mechanisation of pruning can bring real economic benefits by drastically reducing the amount of manual labour required. Pruning machines go further than simple pre-pruning machines by cutting the shoots closer to the cordon, for a two-eye pruning operation supplemented by a quick manual operation to cut the shoots on the sides or under the supporting wire. Another approach to this economic challenge is to mechanise the descent of the wood.Mechanical pruning: first and foremost an economic issue
Irrespective of the type of vine management envisaged, pruning represents a significant cost on farms, due to the manual labour required for the pruning itself, the pulling, the lowering of the wood, the crushing and possibly the tying of the guyot rods. Robotisation of these operations is a way of reducing costs that could be envisaged in the long term if the current methods are to be maintained.The mechanisation of pruning, even partial, can bring real economic benefits by simplifying pruning methods and drastically reducing the amount of manual labour required. This began in the 1980s with pruning machines, which greatly reduced the time and effort involved in pulling the wood, especially from the cordon, but also from the guyot, by freeing the shoots from the trellising wires.
Today's pruning machines go a step further by cutting the shoots closer to the cordon, aiming for a two-eye pruning as soon as the machine passes over, supplemented by a quick manual reshoot to cut the shoots on the sides or under the supporting wire.
The aim is to keep manual labour time to a strict minimum, i.e. 8 to 12 hours per hectare compared with 35 to 50 hours for conventional vine management.
These machines are complementary to (and sometimes combined with) pre-pruning machines, but are only suitable for relatively well-managed rows. In fact, for mechanisation to be as effective as possible, some optimisation is needed in terms of vineyard management.
A vineyard adapted for more efficient pruning mechanisation
Pruning machines can be used on any type of cordon, but when you want to optimise the mechanisation of this operation, it's best to establish the vineyard in a specific way so as to get the most out of it in terms of work organisation, lower costs and the longevity of the vineyard.To make it easier for machines to work close to the cordon, it is essential that the cordon is properly aligned: this makes it easier to set a working height that is easy to maintain , whether or not the cordon is monitored automatically.
This method of pruning the vine generally results in an increase in the bud load on the plot. This results in higher yields if the plot can withstand them, and places greater stress on the trellising than conventional pruning methods. If the mechanical strength of the whole assembly (support wire, ties, stakes) is insufficient, the support wire on which the cordon is wound can, over time, make waves, which is more complicated to follow with the pruning machine or which results in a very variable cutting height and potentially more time spent manually if you want to regulate the bud load a little.
Good mechanical strength of the stumps is important for the quality of the cut and to avoid injury (pulling on the stump). For new plantings, it is therefore recommended that the stumps be tied together by lengthening the cord from one stump to the next.
The height of the support wire for this method is open to discussion (open or closed bearing, etc.), but with a view to reducing and simplifying manual work, ergonomics is a point to be taken into account. With this in mind, raising the support wire so that you don't have to bend down when pruning very quickly is particularly interesting.
Careful establishment of the cordon to limit the number of shoots that the machine cannot cut: when the cordon is formed, the stumps are bent over the support wire; their bend must be gradual (no right angles) and the radius of the bend, like that of the trunk, must be definitive if possible. in this way, no shoots grow below the future cordon on which the machine works.
The positioning of the stakes is important, both in terms of their number (to support the load) and in terms of the care taken to ensure that they are set in relation to the supporting wire in the case of free-standing, to limit impacts with the cutting elements.
The agronomic results of this type of management depend largely on the bud load remaining after manual harvesting.
Quite similar machines with some interesting features
The machines differ in terms of their level of technical sophistication and whether or not they have a pre-pruning module that allows both operations to be carried out simultaneously. The cutting and bead tracking modules can also vary from machine to machine. Finally, there is the option of mounting the machine on a carrier, either at the front of the machine or on its side for better visibility of the cut.Generally speaking, the machines on the market have a lot in common: the aim is to cut above and to the sides of a cordon, and if the trellising wires are kept, to move the cutting elements away from the stakes.
The cutting elements are often circular saws powered by hydraulic or electric motors (Pellenc). Wear and tear depends on the conditions of use, but the cost of replacing or sharpening the saws should be taken into account. These saws require high rotation speeds for a clean cut, and need a hydraulic power unit. The result is a lot of noise and wood splashing, but the cutting capacity is high. There are also machines with alternative cutting bars, which are less noisy and also less powerful when dealing with wood that is several years old, and which produce virtually no splatter.
The opening devices for the passage of the stakes are mostly completely mechanical: rollers are pressed in and force the cutting module supports apart. Given the low forward speed, the mechanical constraints are acceptable.
A few sophisticated systems have been developed to track the bead, either laterally (CGC Agri) or horizontally (Pellenc). The aim is to make it easier to drive the machines by taking some of the pressure off the driver, who has to keep the pruner close to the cordon without taking too many risks. This is an additional factor of precision and optimisation to keep the cutting height low enough and limit the number of subsequent pruning strokes, but it also makes it possible to slightly increase the working speed (up to 2.5 km/h), which without special assistance remains at around 1.5 km/h.
Factors influencing the benefits of the technique: an initial investment that can pay off
The results of mechanical pruning depend on 3 main factors: the machine, the plot and the human being.The machine plays a part in the precision of the work, the comfort of the operator and the work rate, not forgetting the economic aspect of the investment, which varies according to whether or not a pre-pruning module is installed.
Theadaptation of the plot to the technique is a key factor, because while it is possible to work on old cordons or on transformed guyot plots, the precision of the work and the optimisations made possible by a specific vineyard establishment are not achieved. Here too, initial investment in trellising and cordon preparation is required .
Finally, the human factor is a determining factor on a number of points that combine with the previous ones: without assistance in driving and following the cordon, it is more difficult to envisage mechanical pruning over large areas, as it is more strenuous for the driver. The time required for training and preparing the beads for mechanical pruning should not be overlooked, as it represents an additional investment. Finally, the time actually spent by operators on manual harvesting is a factor in controlling costs when it is limited, but it is also a factor in regulating the bud load, so there is a balance to be struck.
Mechanical pruning, an alternative to mechanical pruning for maintaining the pruning method
Other machines can be used specifically to mechanise the pulling and crushing of shoots from Guyot vines, which also offers substantial savings without changing the pruning method or the bud load left at the time of pruning. They can be used in vineyards that have been prepared so that the trellising wires can withstand the tensile forces imposed. The machines can only be used once the pruning (cane, spur) has been carried out.The manufacturers in this field are Clemens, Ero and Provitis.
The differences in machine design relate to the way in which trellising and wood extraction are managed: from above or from the side, and also to the shredding process, which may or may not be integrated into the machine.
A look back at the "TRP equipment" (Precision close pruning) demonstration on 09 March 2023 in Mauriac
This pruning technique is fully in line with a low-cost technical itinerary. It cuts costs by simplifying or eliminating certain tasks, such as mechanised pruning, bending, pulling and crushing wood, and also reduces the incidence of wood diseases.Around 150 winegrowers turned out to see 6 machines in action on one of the vineyard plots that the YON family has been using TRP for a number of years.
6 manufacturers were present: ERO, TERRAL, CELLIER BOISSET, FERRAND, PELLENC and PROVITIS.
Tool prices ranged from €14,000 to €36,000, with the main difference in price being the 'automatic bead tracking' option.
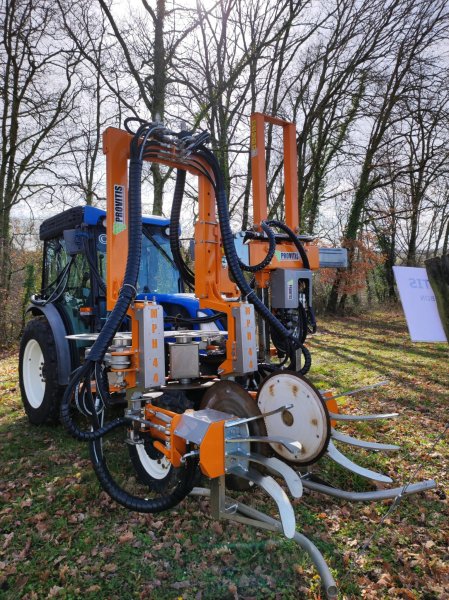
Provitis

Terreal
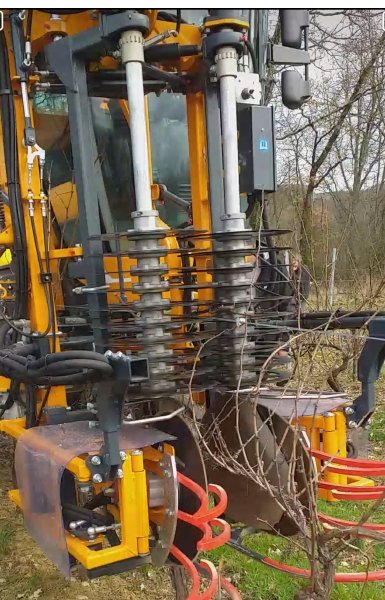
Pellenc
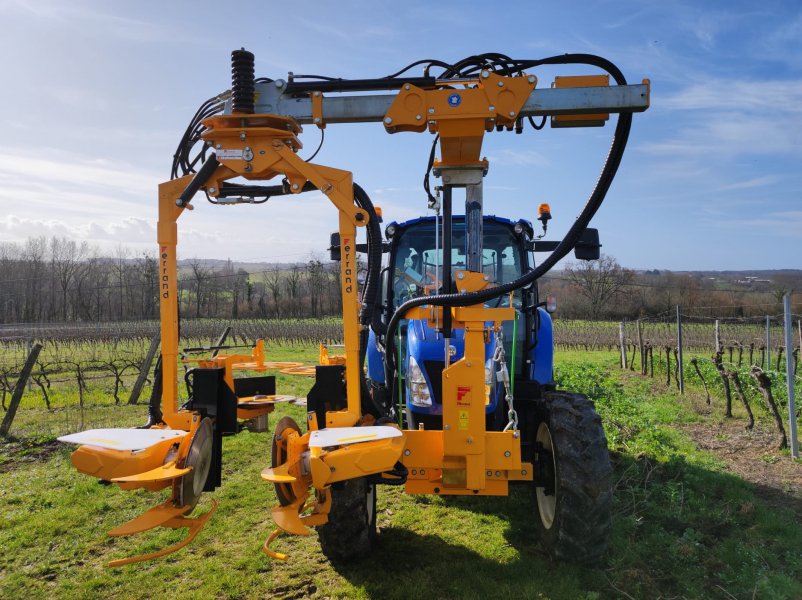
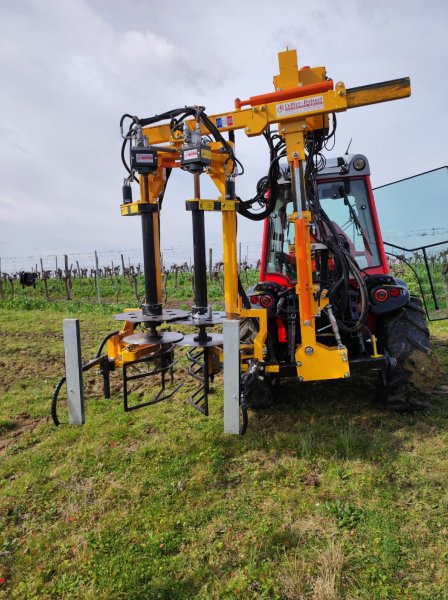
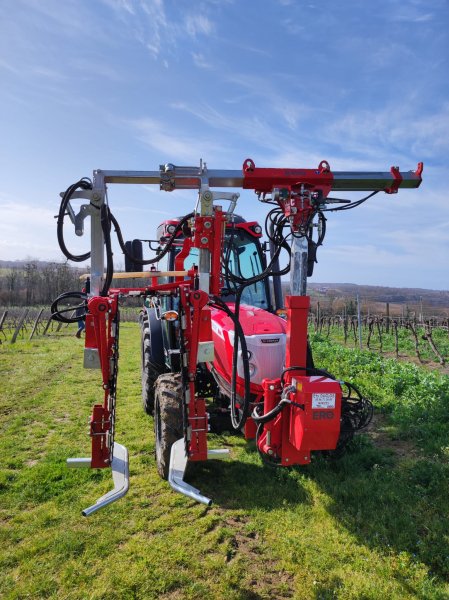
Comparative summary of the equipment presented