Destemmer
Les érafloirs sont des appareils à axe horizontal et cage rotative. Ils ont la fonction d'érafler la vendange préalablement égouttée provenant de récolte manuelle ou mécanique et d'éliminer tout corps étranger pouvant détériorer le matériel placé en aval.
Ils peuvent être utilisés seuls ou associés à une table de tri manuelle placée avant ou après, à une table vibrante d'égouttage ou à un trieur mécanique placé après.
Ils peuvent être utilisés seuls ou associés à une table de tri manuelle placée avant ou après, à une table vibrante d'égouttage ou à un trieur mécanique placé après.
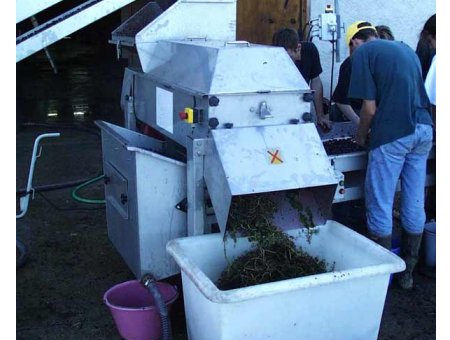
Components of a destemmer
The beaters
The beaters (or hedgehogs) have bars (or rods) arranged in a helix on the rotating shaft. The beaters are made of metal or plastic, sometimes adjustable in orientation and length, and attached to the shaft or not. The axis of the beaters is sometimes eccentric towards the bottom of the cage to make it easier to remove the leaves. Most models have a variable speed drive to regulate rotation speed.- Straight beaters with cylindrical plastic or stainless steel tips have a reduced impact surface on the harvest, compensated for by a larger number of beaters.
- Threshers with plastic or stainless steel inserts, adjustable for inclination, can be used to adjust the impact surface on the grapes and also to change the speed at which the stalks are removed.
- Flat beater blades are often removable, bolted onto the axis of rotation. This arrangement provides a larger surface area for impact on the grapes.
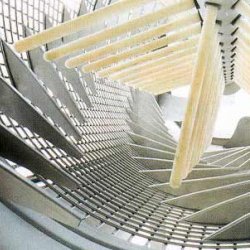
Cylindrical beaters
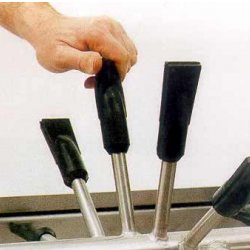
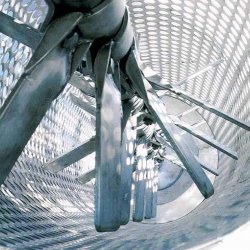
Flat beaters
The rotating cage
The cylindrical openwork cage contains the beaters. The aim is to separate the rejects from the noble products.Rotating cages rotate either in the same direction as the beater, or in the opposite direction. Their rotation speed is around ten times slower than that of the beaters. Some models also incorporate a specific variable speed drive for the cage.
The perforations in the cage for the passage of the bays can be 20 to 35 mm in diameter or width.
Cylindrical cages can be of different types:
- Sheet metal with pressed perforations (or pressed edges) to prevent dilaceration of the stalks
- Interlocking rod assemblies; the elements are removable
- Welded stainless steel mesh with a large surface area of cells
- Woven wire mesh
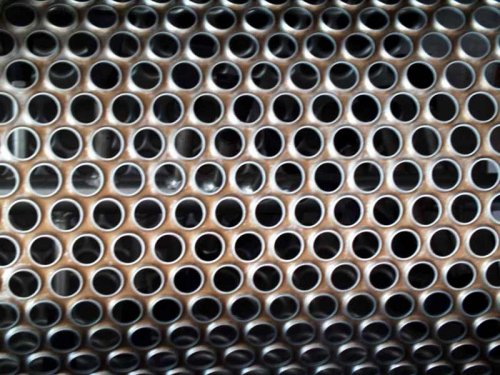
Deep-drawn perforated plate
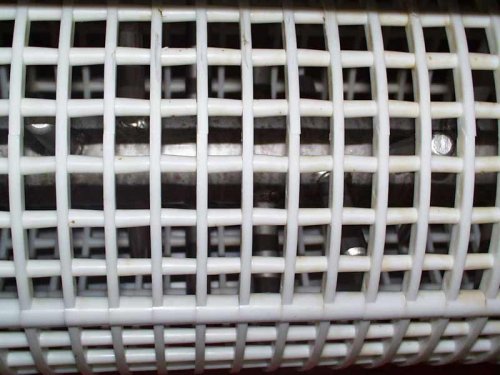
Interlocking rods
The cages are arranged horizontally and rotate continuously. These elements are rotated by electric motors and protected by one or more covers. They are generally fed from a feed hopper .
Optional components
The destemmer can be combined with other equipment such as :- a crusher
Crushing crushes the berries. It is highly recommended for classic red winemaking.
Many destemmer models can be combined, often as an option, with a crusher. The crusher can be incorporated into the destemmer or be removable or retractable.
The crusher is made up of several crenellated rollers. The spacing between the rollers can sometimes be adjusted to suit the size of the berries.
Many destemmer models can be combined, often as an option, with a crusher. The crusher can be incorporated into the destemmer or be removable or retractable.
The crusher is made up of several crenellated rollers. The spacing between the rollers can sometimes be adjusted to suit the size of the berries.
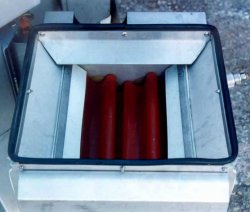
Crusher
- oblique deflectors
- augers
This system is recommended if the destemmer is not supplied at a constant rate.
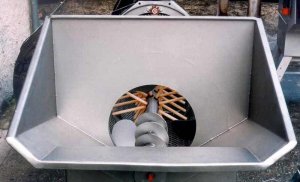
Endless screw
- tapping grids
However, it is not a substitute for the main draining process, which is strongly recommended upstream (skip, conquet, draining table).
- non-draining hatches
- tilt adjustment
Points to bear in mind
Ease of dismantling and cleaning
The ease with which a de-stemmer can be dismantled, cleaned and maintained is an important factor in the hygiene, efficiency and lifespan of an appliance.- Dismantling
Similarly, the equipment must be located so that it can be completely dismantled. Avoid cramped or hard-to-reach places .
Some machines allow the drive elements to be isolated from the harvest circuit to make cleaning easier.
- Cleaning
These cleaning systems slow down the clogging of the cage. However, they do not eliminate the need to dismantle the unit and clean it thoroughly at the end of use (after each day or half-day). This also applies to the cleaning systems themselves (e.g. cleaning the unclogging brush).
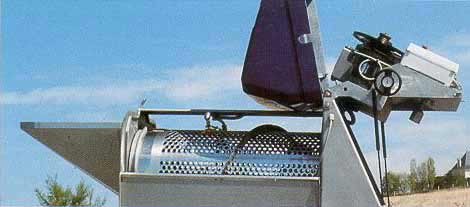
Dismantled scraper
Adapting the flow rate from the reception site according to the input to the vat room
This is a general method but, before any purchase is made, each individual case should be examined carefully with the supplier.- The harvesting and transport yard delivers N tonnes per hour to the vat house.
- The estimated effective working time of the destemmer on the harvest is X%. The rest of the time, which should not be underestimated, consists of adjustment, cleaning, draining, waiting time between two trailers, etc...
The operating capacity of the destemmer should be : N x 100 / X
Example: For an average hourly input of 6 tonnes, and an estimated effective operating rate of 60%, the destemmer throughput should be: 6 x 100 / 60 = 10 t/h
- As the destemmer is the basic piece of equipment, the other machines associated with it downstream should have a throughput around 5% higher. For the same reasons, the feed rates upstream (conquet, trailers, conveyor or sorting table) must be 5% lower than this rate.
- When the basic machine is the sorting table, the nominal flow rate of the destemmer should be 5% higher than that of the sorting table, otherwise the destemmer will be under-fed and its efficiency will be reduced.
- In all cases, it is advisable for all the elements in the chain (belt, conquet, skip or sorting table) to be fitted with variable speed drives, so as to be able to work at the lowest possible throughput. This considerably reduces the amount of crushing of the harvest, which can be detrimental to the quality of the resulting wine.
Supply method
- Choose a model capable of delivering this flow rate at a slow beater rotation speed (e.g. for a required flow rate of 15 t/h, choose a model capable of working at between 12 and 20 t/h).
- For a supply with an irregular flow rate, choose a hopper fitted with a feed screw to regulate the flow rate and improve the quality of the destemming.
- For direct supply by screw trailer or moving floor, a large hopper is preferable.
Type of supply
- To obtain high-quality destemming adapted to the sometimes highly variable characteristics of the different grape varieties, prefer equipment with variable beater speed control.
- Choose a cage with perforations that are well adapted to the grape varieties on the farm.
- For mechanical harvesting, choose equipment with a draining grid. It is strongly recommended that the grapes be completely drained from the bin or cone before destemming.
- For machine-harvested grapes, the model must be extremely robust to ensure that any foreign bodies are removed without damage.
Ease of cleaning, safety and after-sales service
- Choose a machine that can be completely and easily dismantled to facilitate frequent cleaning and maintenance of the equipment.
- For obvious safety reasons, always choose machines fitted with systems that automatically stop the motors if work is carried out on the rotating parts.
- The CE standard is the responsibility of the manufacturer, who uses this label to indicate that its equipment complies with the safety standards laid down by the European Community and the Labour Code.
- A stalk separator breakdown can have catastrophic consequences for your harvest. Don't neglect the quality of your after-sales service.
Position in the reception chain
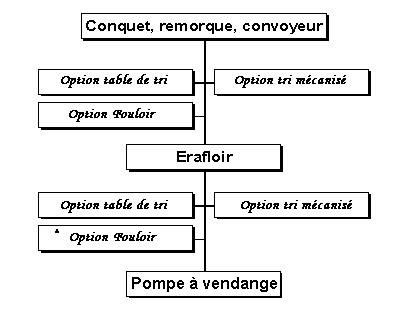
The destemmer is part of the harvest reception chain. The following diagram shows the different ways in which a destemmer can be positioned in this chain.
Experimental work has highlighted the advantages and disadvantages of the different positions of the sorting table or crusher.
Experimental work has highlighted the advantages and disadvantages of the different positions of the sorting table or crusher.
- Sorting table before destemming
- Sorting table after destemming
- Crusher
Method for determining the flow rate required for a reception site, based on the input to the vat room.
Quality control of destemming
Measurements carried out jointly by the Gironde Chamber of Agriculture and IFV Bordeaux-Blanquefort are used to determine the quality of destemmer work. These measurements are carried out on different grape varieties in order to compare the quality of destemming for different grapes. Four criteria are used to determine the quality of destemming alone, without crushing:- efficiency, to assess the destemming capacity of the equipment.
It is calculated as follows
Efficiency % = [(A - B)/A] x 100
A = % of (stalks + miscellaneous debris) in the harvest before destemming (mass)
B = % of (stalks + miscellaneous debris) in the vatted harvest (mass)
This efficiency value should be between 80 and 100% for hand-picked grapes. For mechanically harvested grapes, the percentage by weight of stalks and miscellaneous debris before destemming is often low (2 to 4%). In these cases, the error in weighing results in too great an uncertainty in the estimate of efficiency. This is then judged solely by the percentage of stalks and miscellaneous debris in the vatted harvest:A = % of (stalks + miscellaneous debris) in the harvest before destemming (mass)
B = % of (stalks + miscellaneous debris) in the vatted harvest (mass)
This value must be less than 1%.
- roughness is a measure of the influence of the mechanical action of the machine on the grapes
It is calculated as follows:
Brutality % = [(A - B)/A] x 100
A = % of whole berries in the harvest before destemming (mass)
B = % of whole berries in the harvest before crushing (mass)
There is no recommended value for brutality. It depends enormously on the grape variety, the state of health and the degree of ripeness. It should be as low as possible.
A = % of whole berries in the harvest before destemming (mass)
B = % of whole berries in the harvest before crushing (mass)
- the percentage of berries in the rejects
Percentage of berries in shoots
% Berries = [A / B] x 100
A = Mass of berries in the shoots
B = Mass of shoots.
This percentage must be as low as possible for obvious economic reasons. 0.5% of berries in the rejects represents approximately 0.4 g per kg of destemmed grapes, i.e. 40 L of wine for a winery producing 1000 hL of wine
A = Mass of berries in the shoots
B = Mass of shoots.
- visual inspection of the state of dilaceration of the stalks
There are no constant values for these four criteria for any given piece of equipment. To optimise each of them, the destemmer should be adjusted during the campaign, depending on the following factors:
- Berry ripeness: Very ripe grapes are sensitive to rough handling.
- The grape variety : The resistance of the berries to bursting varies according to the grape variety. In addition, the berries hold on to the stalk more or less well, depending on their ripeness.
- Supply rate: To obtain good quality destemming, it is imperative that the feed is constant and well adapted to the flow rate of the machine.
- The quality of the harvest before destemming: Efficiency also depends on the level of impurities in the harvest and its health.
Safety
Safety is an essential aspect of any machine with rotating parts. Machines fitted with an emergency stop button, or better still, automatic stop devices when the side covers are operated, are a must. As a general rule, all new equipment must comply with the new European safety regulations. The CE mark must appear clearly on the appliance and on the instructions for use and maintenance that must be supplied when the appliance is purchased. From 1 January 1997, all machines used in cellars, whether new or old, must comply with the French Labour Code (Articles R 233-15 to R 233-30). A description of these standards can be obtained from the Caisses Régionales de Mutualité Sociale Agricole.Please note: These standards also apply to second-hand equipment. In the event of an accident, the seller - even a private individual - is criminally liable for the non-conformity of the equipment sold.
Malfunctions : Questions and answers
My destemmer doesn't remove enough stalks
The equipment is insufficiently or irregularly fed:→ increase or regulate the flow rate to the destemmer.
The speed of rotation of the beaters is not sufficient:
→ increase the speed of rotation.
The stalks or portions of stalks pass through the perforations in the end part of the cage, which is too long:
→ obstruct this part of the cage using a "sock" provided by some manufacturers.
The perforations in the cage are too large and allow cobs to pass through:
→ contact the manufacturer to install a cage with smaller perforations on your model
The stalks are diluted by my destemmer
The speed of the beaters is too high:→ reduce the speed, while checking that the efficiency remains correct.
The supply or discharge rate is not sufficient, the stalks stay too long in the cage and are dilacerated:
→ check that there is no blockage in the stalk discharge ;
→ if necessary, increase the feed rate.
The cage used may have too many sharp corners:
→ contact the manufacturer to install another type of cage.
I have a lot of berries in the rejects
The beater speed is not fast enough:→ increase the speed while checking that the stalks are not too dilated.
The cage is clogged:
→ stop the destemmer, open and clean the cage.
The cage perforations have too small a cross-section for the berries to pass through:
→ check with the manufacturer whether it is possible to install a cage with larger cross-section perforations on your model.
The appliance is not horizontal but inclined excessively towards the discharge:
→ change the inclination of the appliance (high point at the stalk discharge).
I have a blockage in the destemmer hopper
The beaters are not turning in the right direction→ stop the destemmer and check the electrical connection.
The feed rate is too high :
→ reduce it.
The cage is clogged: stop the destemmer;
→ open and clean the cage.
There is a clog in the stalk discharge :
→ evacuate the cobs more quickly.
Experiment
See the list of experimentsSee more